Application of micro injection molding technique for preparing tungsten-base alloy product and micro injection molding method of tungsten-base alloy powder
A technology of tungsten-based alloy and forming technology, applied in the application of micro-injection molding technology in the preparation of tungsten-based alloy products, in the field of tungsten-based alloy powder micro-injection molding, it can solve the difficulty of MIM forming, many microstructures and micro-sizes, zero The complex structure of components and other problems can reduce pollution, increase bonding force and improve strength.
- Summary
- Abstract
- Description
- Claims
- Application Information
AI Technical Summary
Problems solved by technology
Method used
Examples
Embodiment 1
[0035] 94wt% W, 4wt% Cu, and 2wt% Ni were mixed on a planetary ball mill for 1 hour, and the binders were: 44wt% paraffin, 48wt% polyethylene, and 8wt% surface modifier. On the kneader, knead at 160 degrees for 1 hour, then granulate, and then injection molding, the injection pressure is 100 MPa, the mold temperature is 60 degrees, the injection temperature is 140 degrees, and the mold is demoulded when the mold temperature drops to 35 degrees. Degrease in n-heptane solvent for 4 hours, then heat degrease in degreasing furnace, use H 2 Atmosphere, the heating curve is: heating from room temperature to 400 degrees at a rate of 3 degrees per minute, and holding for 1 hour; then heating at a temperature of 2 degrees to 800 degrees, and holding for 2 hours. The sintering is carried out in a vacuum furnace with an inner pressure of 10Pa, the sintering temperature is 1450° C. and the temperature is kept at the sintering temperature for 80 minutes. Finally, miniature 94wt%W, 4wt%Cu,...
Embodiment 2
[0037] 92wt% WC and 8wt% Co were mixed on a planetary ball mill for 2 hours, and the binders were: 46wt% paraffin, 48wt% polyethylene, and 6wt% surface modifier. On the kneader, knead at 160 degrees for 1 hour, then granulate, injection molding (injection pressure 140MPa, mold temperature 60 degrees, injection temperature is 150 degrees), demoulding when the mold temperature drops to 40 degrees. Degrease in n-heptane solvent for 5 hours, then heat degrease in degreasing furnace, use H 2 Atmosphere, the heating curve is: heating from room temperature to 300 degrees at a rate of 3 degrees per minute, and holding for 1 hour; then heating at a temperature of 2 degrees to 800 degrees, and holding for 2 hours. The sintering is carried out in a vacuum furnace with an inner pressure of 1Pa, the sintering temperature is 1450° C. and the temperature is kept at the sintering temperature for 120 minutes. Finally, miniature 92wt% WC, 8wt% Co alloy parts are obtained.
Embodiment 3
[0039] 90wt% WC and 10wt% Co were mixed on a planetary ball mill for 2 hours, and the binders were: 45wt% paraffin, 48wt% polyethylene, and 7wt% surface modifier. On the kneader, knead at 160 degrees for 1 hour, then granulate, injection molding (injection pressure 120MPa, mold temperature 60 degrees, injection temperature is 145 degrees), demoulding when the mold temperature drops to 35 degrees. Degrease in n-heptane solvent for 5 hours, then heat degrease in degreasing furnace, use H 2 Atmosphere, the heating curve is: heating from room temperature to 300 degrees at a rate of 3 degrees per minute, and holding for 1 hour; then heating at a temperature of 2 degrees to 780 degrees, and holding for 2 hours. The sintering is carried out in a vacuum furnace with an inner pressure of 1Pa, the sintering temperature is 1420° C. and the temperature is kept at the sintering temperature for 90 minutes. Finally, miniature 90wt% WC, 10wt% Co alloy parts are obtained.
PUM
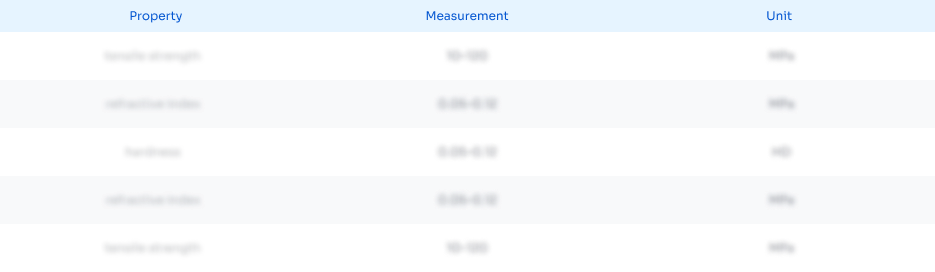
Abstract
Description
Claims
Application Information

- R&D
- Intellectual Property
- Life Sciences
- Materials
- Tech Scout
- Unparalleled Data Quality
- Higher Quality Content
- 60% Fewer Hallucinations
Browse by: Latest US Patents, China's latest patents, Technical Efficacy Thesaurus, Application Domain, Technology Topic, Popular Technical Reports.
© 2025 PatSnap. All rights reserved.Legal|Privacy policy|Modern Slavery Act Transparency Statement|Sitemap|About US| Contact US: help@patsnap.com