Method for preparing polyamide resin used for water color ink
A technology of polyamide resin and water-based ink, which is applied in the field of polyamide resin, can solve the problems of complex preparation methods of water-based polyamide resin and the inability to obtain low VOC, and achieve the effects of environmental friendliness, increased added value, and mild reaction conditions
- Summary
- Abstract
- Description
- Claims
- Application Information
AI Technical Summary
Problems solved by technology
Method used
Image
Examples
Embodiment 1
[0039] (1) Preparation of Hydroxypolyamide
[0040] In a 500ml three-neck flask equipped with a heating mantle, a stirring device, and a thermometer, add 1 mol of carboxy-terminated polyamide with a molecular weight of 2000 to 4000, 1.05 mol of ethylene glycol diglycidyl ether (epoxy 669) and 0.5‰ of epoxy mass Tetraethylammonium chloride was used as a catalyst, and then nitrogen gas was introduced, the temperature was raised to 90°C, and the reaction was stirred at 300 rpm for 1 hour to obtain hydroxyl polyamide.
[0041] (2) Preparation of hydroxypolyamide ester
[0042] In a 500ml three-neck flask equipped with a heating mantle, a stirring device, and a thermometer, use toluene as a solvent, add 1 mol of hydroxypolyamide obtained in step (1), 2 mol of phthalic anhydride polyester polyol and the total mass of hydroxypolyamide and polyester polyol 2% sulfuric acid was used as a catalyst, nitrogen gas was passed, and the mixture was stirred and reacted at 50° C. at a speed of...
Embodiment 2
[0047] (1) Preparation of Hydroxypolyamide
[0048] In a 500ml three-neck flask equipped with a heating mantle, a stirring device, and a thermometer, add 1 mol of adipic acid, a mixture of low molecular weight polyamides with carboxyl groups, and 1.07 mol of bisphenol A diglycidyl ether (E-51, epoxy value 0.51) , ethylene glycol diglycidyl ether (epoxy 669) and dimethylaniline accounting for 1‰ of the mass of epoxy as a catalyst, then nitrogen gas was introduced, the temperature was raised to 100°C, and the reaction was stirred at 300 rpm for 1 hour to obtain hydroxyl polyamide.
[0049] (2) Preparation of hydroxypolyamide ester
[0050] In a 500ml three-neck flask equipped with a heating mantle, a stirring device, and a thermometer, use tetrahydrofuran as a solvent, add 1 mol of hydroxypolyamide obtained in step (1), 2 mol of phthalic anhydride polyester polyol and the total mass of hydroxypolyamide and polyester polyol 1.5% aluminum trichloride was used as a catalyst, nitr...
Embodiment 3
[0054] (1) Preparation of Hydroxypolyamide
[0055] In a 500ml three-necked flask equipped with a heating mantle, a stirring device, and a thermometer, add 1mol of tung oil dimer acid, a mixture of low-molecular-weight-terminated carboxyl polyamides, and 1.1mol of bisphenol A diglycidyl ether (E-44, with an epoxy value of 0.44 ) and triethylamine accounting for 1.5‰ of the mass of epoxy as a catalyst, then nitrogen gas was introduced, the temperature was raised to 120°C, and the reaction was stirred at 300 rpm for 1.5h to obtain hydroxyl polyamide.
[0056] (2) Preparation of hydroxypolyamide ester
[0057] In a 500ml three-neck flask equipped with a heating mantle, a stirring device, and a thermometer, use xylene as a solvent, add 1 mol of hydroxypolyamide obtained in step (1), 2 mol of phthalic anhydride polyester polyol and the total amount of hydroxypolyamide and polyester polyol 1% by mass of boron trifluoride is used as a catalyst, nitrogen gas is passed, and the mixtur...
PUM
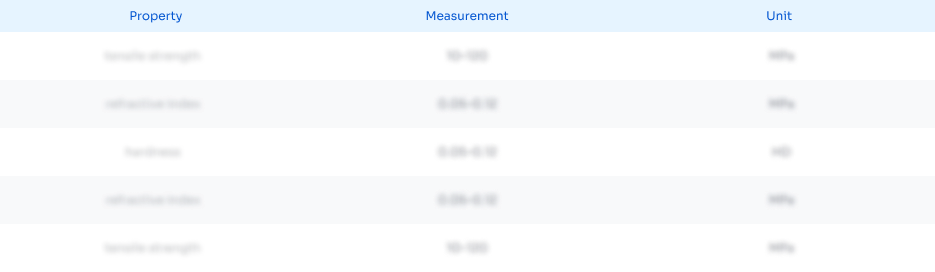
Abstract
Description
Claims
Application Information

- R&D
- Intellectual Property
- Life Sciences
- Materials
- Tech Scout
- Unparalleled Data Quality
- Higher Quality Content
- 60% Fewer Hallucinations
Browse by: Latest US Patents, China's latest patents, Technical Efficacy Thesaurus, Application Domain, Technology Topic, Popular Technical Reports.
© 2025 PatSnap. All rights reserved.Legal|Privacy policy|Modern Slavery Act Transparency Statement|Sitemap|About US| Contact US: help@patsnap.com