Process for treating top gas of reduction shaft furnace
A furnace top gas and treatment process technology, applied in the field of metallurgical chemistry, can solve the problems of energy consumption, water consumption, increased investment, excessive waste gas, and slow heating speed of hot blast stoves, so as to reduce investment costs and operating energy consumption. The effect of improving energy consumption and saving coal consumption
- Summary
- Abstract
- Description
- Claims
- Application Information
AI Technical Summary
Problems solved by technology
Method used
Image
Examples
Embodiment Construction
[0023] An embodiment of the present invention will be further described below in conjunction with accompanying drawing:
[0024] The process includes 8 sub-process systems, namely: 1) coarse dust removal system; 2) primary cooling system; 3) fine dust removal system; 4) secondary cooling system; 5) decarburization system and decompression system; 6) pressurization system; 7) high-pressure gas storage system; 8) two-step heating system. The above-mentioned 8 process systems are connected together through transmission pipelines and transmission devices, and finally the gas with high reduction degree is sent to the direct reduction furnace.
[0025] The system flow is as follows:
[0026] Reduction shaft furnace top gas ① first passes through a coarse dust removal system such as a hot cyclone dust collector for rough dust removal, and then the gas ② enters a primary cooling system such as a heat pipe heat exchanger for heat energy recovery. The by-product is medium-pressure stea...
PUM
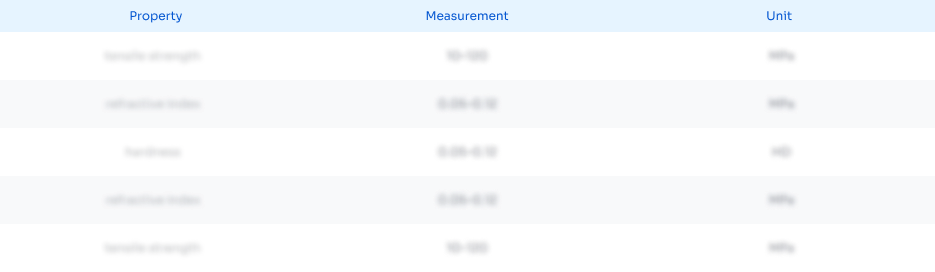
Abstract
Description
Claims
Application Information

- Generate Ideas
- Intellectual Property
- Life Sciences
- Materials
- Tech Scout
- Unparalleled Data Quality
- Higher Quality Content
- 60% Fewer Hallucinations
Browse by: Latest US Patents, China's latest patents, Technical Efficacy Thesaurus, Application Domain, Technology Topic, Popular Technical Reports.
© 2025 PatSnap. All rights reserved.Legal|Privacy policy|Modern Slavery Act Transparency Statement|Sitemap|About US| Contact US: help@patsnap.com