Method for improving performances of resin abrasive tools through carbon nano-tubes
A technology of carbon nanotubes and single-walled carbon nanotubes, applied in abrasives, grinding devices, manufacturing tools, etc.
- Summary
- Abstract
- Description
- Claims
- Application Information
AI Technical Summary
Problems solved by technology
Method used
Examples
Embodiment 1
[0016] Add 3% of carboxylated carbon nanotubes, 22% of modified phenolic resin powder, 30% of copper powder, 10% of chromium oxide, 20% of iron oxide, 18% of silicon carbide micropowder, diamond powder (grain size 120 / 140, concentration 75%) ), mix powder and mix evenly, cold press molding, heat up to 200°C in stages, and heat-preserve and solidify for 10 hours. Compared with the abrasive block without carboxylated carbon nanotube resin under the same process conditions, the service life of the abrasive block can be increased by about 11%.
Embodiment 2
[0018] By adding 3% of hydroxylated carbon nanotubes, 22% of modified phenolic resin powder, 30% of copper powder, 10% of chromium oxide, 20% of iron oxide, 18% of silicon carbide micropowder, diamond powder (grain size 120 / 140, concentration 75%) ), mix powder and mix evenly, cold press molding, heat up to 200°C in stages, and heat-preserve and solidify for 10 hours. Compared with the abrasive block without carboxylated carbon nanotube resin under the same process conditions, the service life of the abrasive block can be increased by about 16%.
PUM
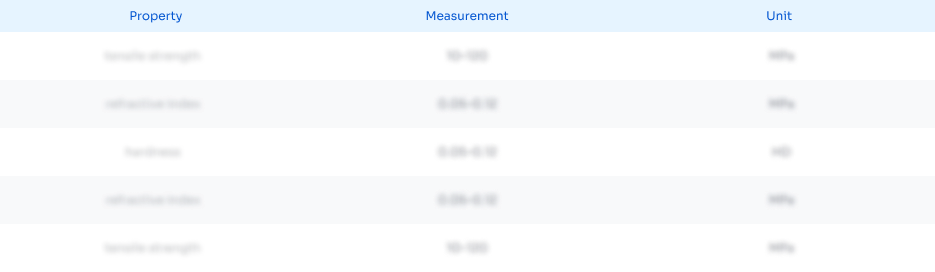
Abstract
Description
Claims
Application Information

- R&D Engineer
- R&D Manager
- IP Professional
- Industry Leading Data Capabilities
- Powerful AI technology
- Patent DNA Extraction
Browse by: Latest US Patents, China's latest patents, Technical Efficacy Thesaurus, Application Domain, Technology Topic, Popular Technical Reports.
© 2024 PatSnap. All rights reserved.Legal|Privacy policy|Modern Slavery Act Transparency Statement|Sitemap|About US| Contact US: help@patsnap.com