Compound centrifugal manufacturing method for axial sleeve of bushing
A technology of centrifugal compounding and manufacturing method, applied in coating, metal material coating process, hot dip plating process, etc., can solve the problems of limited thickness of spray coating, rough wear surface and cracking of surface sprayed materials
- Summary
- Abstract
- Description
- Claims
- Application Information
AI Technical Summary
Problems solved by technology
Method used
Image
Examples
Embodiment 1
[0038] The bottom layer of the centrifugally compounded sinking roller and stabilizing roller bushing is made of 00cr17Ni14Mo2 stainless steel, and the chemical composition is C≤0.03%, Cr16%-18%, Ni10%-14%, Mo2.00%-3.00%, and Mn≤2.00%, Si≤1.00%; the working surface layer is a cobalt-based alloy, and the cobalt-based alloy contains: Si 0.5%, Mn 0.3%, C 0.6%, Al 0.5%, P<0.07%, S <0.07%, V 0.1%, Ti 0.1%, Cr25%, Fe6%, Ni5%, Nb1.5%, W 3%, Mo3%, and the rest is Co. The service time of the bearing pad and sleeve in the prior art is significantly lower than that of the bearing pad and sleeve of the present invention in the same unit, and the service time of the bearing pad and sleeve of the present invention is more than three times that.
Embodiment 2
[0040] Centrifugal composite sinking roller and stabilizing roller bushing bottom layer substrate is austenitic heat-resistant stainless steel SUS316, chemical composition is C≤0.08%, Cr 16%-18%, Ni 10%-14%, Mo 2.00%-3.00% , Mn≤2.00%, Si≤1.00%; the working surface layer is a cobalt-based alloy, and the composition of the cobalt-based alloy is: Al 0.5%, Si 0.4%, Mn 0.7%, C 0.6%, Cr 20%, Fe 12%, Ni 3%, Nb 1.0%, W5%, Mo 2%, V0.2%, Ti0.2%, and the balance is Co. The service time of the bearing pad and sleeve in the prior art is significantly lower than that of the bearing pad and sleeve of the present invention in the same unit, and the service time of the bearing pad and sleeve of the present invention is more than three times that.
Embodiment 3
[0042] Centrifugal composite sinking roller and stabilizing roller bushing bush bottom substrate is heat-resistant stainless steel ZG07Cr19Ni9, chemical composition is C0.07%, Cr18-21%, Ni8.0-11.0%, Mn1.5%, Si1.5%, P ≤0.040%, S≤0.030%; the working surface layer is a cobalt-based alloy, and the composition of the cobalt-based alloy is: Al 0.8%, Si 1.0%, C 1.5%, Mn 0.7%, Cr26%, Fe 12%, Ni 3% , Nb 1.0%, W5%, Mo 2%, V0.2%, Ti0.2%, and the rest is Co. The service time of the bearing pad and sleeve in the prior art is significantly lower than that of the bearing pad and sleeve of the present invention in the same unit, and the service time of the bearing pad and sleeve of the present invention is more than three times that.
[0043] Figure 6A A photograph showing the corrosion resistance of a bearing pad bushing according to the invention. Figure 6A It is the appearance of the interface of the cobalt-based alloy according to the present invention after being soaked in the hot-di...
PUM
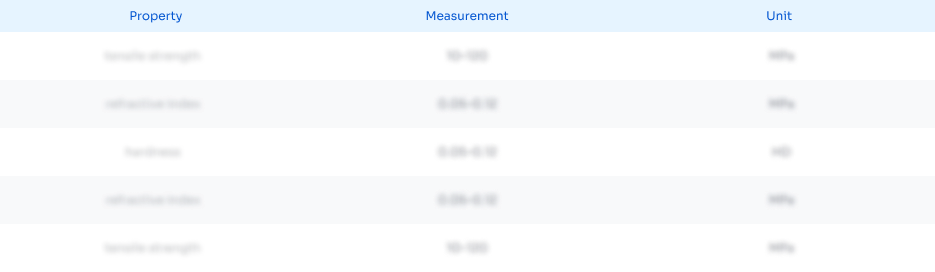
Abstract
Description
Claims
Application Information

- R&D
- Intellectual Property
- Life Sciences
- Materials
- Tech Scout
- Unparalleled Data Quality
- Higher Quality Content
- 60% Fewer Hallucinations
Browse by: Latest US Patents, China's latest patents, Technical Efficacy Thesaurus, Application Domain, Technology Topic, Popular Technical Reports.
© 2025 PatSnap. All rights reserved.Legal|Privacy policy|Modern Slavery Act Transparency Statement|Sitemap|About US| Contact US: help@patsnap.com