High-temperature resistant coating and preparation method thereof
A high-temperature-resistant coating and batching technology, applied in the coating field, can solve the problems of large metal loss, coarse surface grains, and high price in flame cleaning, and achieve the effects of improving metal yield, simple production process, and low production cost
- Summary
- Abstract
- Description
- Claims
- Application Information
AI Technical Summary
Problems solved by technology
Method used
Examples
Embodiment 1
[0026] First get 50 kilograms of 400 mesh quartz powder and 40 kilograms of water glass and stir to make a mixture, then add 5 kilograms of water to the mixture and stir to make a slurry, then add 5 kilograms of calcium polyacrylate to the slurry and stir evenly, Promptly make a kind of high temperature resistant coating of the present invention.
Embodiment 2
[0028] First get 70 kilograms of 450 mesh quartz powder and 20 kilograms of water glass and stir evenly to make a mixture, then add 4 kilograms of water to the mixture and stir to make a slurry, then add 6 kilograms of urea-formaldehyde resin to the slurry and stir evenly, namely A high temperature resistant coating of the present invention is obtained.
Embodiment 3
[0030] First get 60 kilograms of 500 mesh quartz powders, 30 kilograms of water glass and stir to make a mixture, then add 6 kilograms of water to the mixture and stir to make a slurry, then add 4 kilograms of melamine formaldehyde resin to the slurry and stir, Promptly make a kind of high temperature resistant coating of the present invention.
PUM
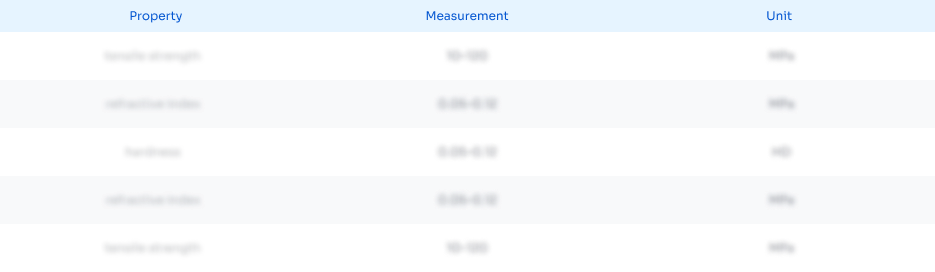
Abstract
Description
Claims
Application Information

- R&D
- Intellectual Property
- Life Sciences
- Materials
- Tech Scout
- Unparalleled Data Quality
- Higher Quality Content
- 60% Fewer Hallucinations
Browse by: Latest US Patents, China's latest patents, Technical Efficacy Thesaurus, Application Domain, Technology Topic, Popular Technical Reports.
© 2025 PatSnap. All rights reserved.Legal|Privacy policy|Modern Slavery Act Transparency Statement|Sitemap|About US| Contact US: help@patsnap.com