Process for producing low-alloy high-strength medium plate with 0 to 0.05 percent of arsenic content
A low-alloy high-strength, production process technology, applied in temperature control and other directions, can solve the problems of spherical carbide inclusion precipitation, low drop-weight tearing performance qualification rate, reduced steel impact toughness, etc., to achieve stable microstructure and mechanical properties. , Stable drop hammer tearing performance, stable performance effect
- Summary
- Abstract
- Description
- Claims
- Application Information
AI Technical Summary
Problems solved by technology
Method used
Image
Examples
Embodiment 1
[0016] A production process for low-alloy high-strength medium-thick steel plates with an arsenic content of 0-0.05%. The arsenic content is 0.016%. 830°C, cumulative total deformation ≥ 60%, slow cooling in air to 750°C after final rolling, then rapid cooling to 500°C at 15°C / s, and keep warm. The precipitation of carbides in the product is as follows figure 2 shown.
Embodiment 2
[0018] A production process of low-alloy high-strength medium-thick steel plate with arsenic content of 0-0.05%. The arsenic content is 0.016%. Cumulative total deformation ≥ 60%, slow cooling in air to 700°C after final rolling, then rapid cooling to 400°C at 15°C / s, and keep warm.
Embodiment 3
[0020] A production process of low-alloy high-strength medium-thick steel plate with arsenic content of 0-0.05%. The arsenic content is 0.016%. After the medium-thick steel plate is kept warm at 1100°C, it undergoes rough rolling and finish rolling, and the final rolling temperature is 870°C. , cumulative total deformation ≥ 60%, slow cooling in air to 730°C after final rolling, and then rapid cooling to 450°C at 20°C / s, then keep warm.
PUM
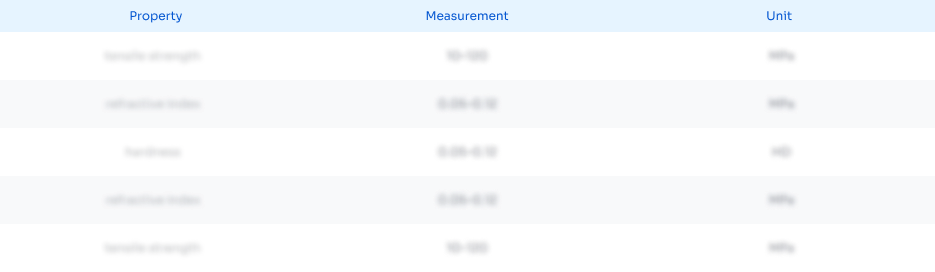
Abstract
Description
Claims
Application Information

- R&D
- Intellectual Property
- Life Sciences
- Materials
- Tech Scout
- Unparalleled Data Quality
- Higher Quality Content
- 60% Fewer Hallucinations
Browse by: Latest US Patents, China's latest patents, Technical Efficacy Thesaurus, Application Domain, Technology Topic, Popular Technical Reports.
© 2025 PatSnap. All rights reserved.Legal|Privacy policy|Modern Slavery Act Transparency Statement|Sitemap|About US| Contact US: help@patsnap.com