Catalyst for hydrolyzing carbonyl sulfur and preparation method thereof
A carbonyl sulfide catalyst and oxide technology, which is applied in the direction of catalyst activation/preparation, chemical instruments and methods, physical/chemical process catalysts, etc., can solve the problems of long process flow, large energy consumption, and low application range of removal concentration
- Summary
- Abstract
- Description
- Claims
- Application Information
AI Technical Summary
Problems solved by technology
Method used
Examples
preparation example Construction
[0018] Catalyst preparation method of the present invention comprises the steps:
[0019] 1. Activated carbon can be coal or coconut shell activated carbon: wash it with tap water and distilled water and dry it at 110-120°C for 2-4 hours.
[0020] 2. Boil the cleaned activated carbon with 1mol / L KOH solution for 1.5~2h for modification, and then wash it with distilled water until the pH is around 6.0.
[0021] 3. Select one or more metal salt solutions to impregnate the above-mentioned activated carbon for modification. The metal salt can be Al(NO 3 ) 3 , Cu(NO 3 ) 2 , Fe(NO 3 ) 3 , Mg(NO 3 ) 2 , Ce(NO 3 ) 3 , Zn(NO 3 ) 2 One or more of them are ultrasonically impregnated for 0.5-1 hour, the impregnating content is 10-90% (mass ratio) of activated carbon, and the volume of impregnating liquid is: 10g of catalyst plus 20ml of impregnating liquid.
[0022] 4. Dry the impregnated activated carbon in a constant temperature drying oven at 120°C for 2-6 hours, and then d...
Embodiment 1
[0024] Example 1: Take 5.0 g of coal-based activated carbon and grind it into 40-60 meshes, wash it with tap water and distilled water three times, then boil it with 1 mol / L KOH solution for 1.5 hours, and dry it in a constant temperature drying oven at 120°C for 3 hours. Weigh 1.84g of Al(NO 3 ) 3 The solid was dissolved in 10.0ml of distilled water, then the activated carbon was ultrasonically impregnated for 0.5h, then dried in a constant temperature drying oven at 120°C for 3 hours, and then heated in a tube furnace at 400°CN 2 Activation under protection for 3 hours. Then weigh 0.50g of Na 2 CO 3 Dissolved in 10.0ml of distilled water, the activated carbon after roasting in Na 2 CO 3 Soak in the solution for 0.5h, and dry in a constant temperature drying oven at 120°C for 3 hours. The reaction conditions are catalyst 1.00g, temperature 50°C, space velocity 1000h -1 , COS concentration 500ppm, oxygen concentration 0.5%. The catalyst was installed in a fixed-bed rea...
Embodiment 2
[0026] Example 2: Take 3.0 g of coal-based activated carbon and grind it into 40-60 meshes, wash it three times with tap water and distilled water respectively, then boil it with 1 mol / L KOH solution for 1.5 hours, and dry it in a constant temperature drying oven at 120°C for 3 hours. Weigh 0.76g of Fe(NO 3 ) 3 The solid was dissolved in 6.0ml of distilled water, then ultrasonically impregnated activated carbon for 0.5h, and then dried in a constant temperature drying oven at 120°C for 3 hours, and then dried in a tube furnace at 500°CN 2Activation under protection for 3 hours. Then weigh 0.24g of Na 2 C0 3 Dissolved in 6.0ml of distilled water, the activated carbon after roasting in Na 2 CO 3 Soak in the solution for 0.5h, and dry in a constant temperature drying oven at 120°C for 3 hours. The reaction conditions are catalyst 1.00g, temperature 50°C, space velocity 1000h -1 , COS concentration 550ppm, oxygen concentration 0.5%. The catalyst was installed in a fixed-be...
PUM
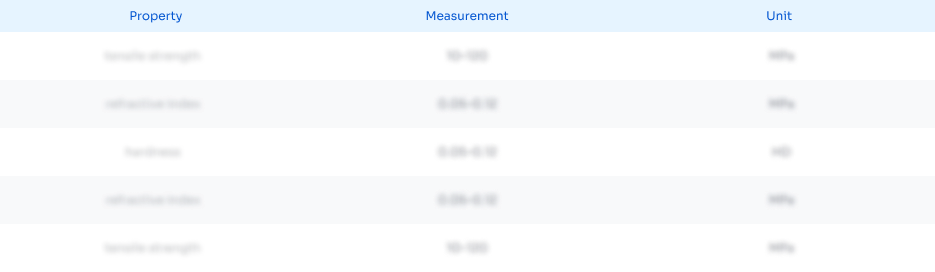
Abstract
Description
Claims
Application Information

- R&D
- Intellectual Property
- Life Sciences
- Materials
- Tech Scout
- Unparalleled Data Quality
- Higher Quality Content
- 60% Fewer Hallucinations
Browse by: Latest US Patents, China's latest patents, Technical Efficacy Thesaurus, Application Domain, Technology Topic, Popular Technical Reports.
© 2025 PatSnap. All rights reserved.Legal|Privacy policy|Modern Slavery Act Transparency Statement|Sitemap|About US| Contact US: help@patsnap.com