Process for manufacturing high bonding strength copper clad aluminum wire
A technology of copper-clad aluminum row and bonding strength, which is applied in the direction of manufacturing tools, metal processing equipment, non-electric welding equipment, etc., can solve the problems of copper-aluminum delamination, low interface bonding strength between copper and aluminum, and poor machinability. Achieve the effect of ensuring reliability and improving interface bonding strength
- Summary
- Abstract
- Description
- Claims
- Application Information
AI Technical Summary
Problems solved by technology
Method used
Image
Examples
Embodiment 1
[0031] The manufacturing process of the copper-clad aluminum bar with high bonding strength of this embodiment comprises the following steps: 1) explosive welding: as figure 1 As shown, the aluminum plate 2 as the substrate, the support ring 3, the copper plate 4 as the cladding plate, and the explosive 5 are stacked on the foundation 1 from bottom to top, and then the explosive 5 is detonated, and the copper plate 4 hits the aluminum plate 2 at high speed, and the two are welded together. , to obtain the copper-aluminum composite panel blank 6 (such as figure 2 shown); 2) roll the copper-aluminum composite plate into a tubular shape, with the copper layer outside, weld the longitudinal seam, then press and form, carry out stress-relief annealing and polishing at a temperature of 350-450°C and a holding time of 30-60min, and obtain Copper clad aluminum row.
Embodiment 2
[0033] The manufacturing process of the copper-clad aluminum bar with high bonding strength in this embodiment includes the following steps: 1) Explosive welding: on the foundation 1, the aluminum plate 2 as the substrate, the support ring 3, and the copper plate 4 as the cladding plate are stacked sequentially from bottom to top and Dynamite 5 (eg figure 1 Shown), detonate explosives 5 then, copper plate 4 impacts aluminum plate 2 at high speed, the two are welded as a whole, obtain copper-aluminum composite plate blank 6 (such as figure 2 shown); 2) the copper-aluminum composite plate 6 is rolled into a tubular shape, the copper layer 4 is outside, the longitudinal seam is welded, and then the molten aluminum 7 is poured to make a copper-clad aluminum rod (such as image 3 shown), then press molding, stress relief annealing and polishing at a temperature of 350-450° C. and a holding time of 30-60 minutes to obtain a copper-clad aluminum row.
Embodiment 3
[0035] The manufacturing process of the high bonding strength copper-clad aluminum bar of this embodiment includes the following steps: 1) Explosive welding: on the basis, the copper plate as the substrate, the support ring, the aluminum plate as the cladding plate and the explosive are stacked sequentially from bottom to top, and then Explosives are detonated, and the aluminum plate impacts the copper plate at a high speed, and the two are welded together to obtain the copper-aluminum composite plate blank; Figure 4 shown), then folded and pressed in half, with the copper layer on the outside, welded the longitudinal seam, and then carried out stress-relief annealing and polishing at a temperature of 350-450°C and a holding time of 30-60min to obtain a copper-clad aluminum row.
PUM
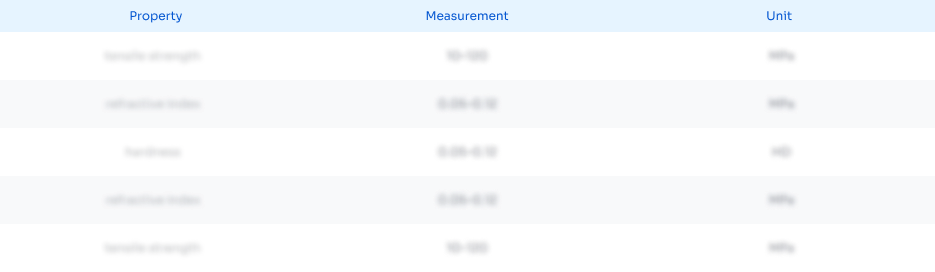
Abstract
Description
Claims
Application Information

- R&D Engineer
- R&D Manager
- IP Professional
- Industry Leading Data Capabilities
- Powerful AI technology
- Patent DNA Extraction
Browse by: Latest US Patents, China's latest patents, Technical Efficacy Thesaurus, Application Domain, Technology Topic, Popular Technical Reports.
© 2024 PatSnap. All rights reserved.Legal|Privacy policy|Modern Slavery Act Transparency Statement|Sitemap|About US| Contact US: help@patsnap.com