Apparatus and method for producing high-purity sulphur glass
A technology of chalcogenide glass and preparation device, applied in glass manufacturing equipment, glass furnace equipment, manufacturing tools, etc., can solve the problems of unpublished data, increase light scattering loss, reduce glass transmittance, etc., and achieve infrared transmittance Good, uniform optical quality
- Summary
- Abstract
- Description
- Claims
- Application Information
AI Technical Summary
Problems solved by technology
Method used
Image
Examples
Embodiment 1
[0012] Embodiment 1: As shown in the figure, a high-purity chalcogenide glass preparation device includes a swing furnace body 1 and a quartz ampoule 2 with the function of swinging back and forth in the Z direction. The swing furnace body 1 is provided with a first furnace chamber 11 and a second furnace chamber. Two furnaces 12, the first furnace 11 and the second furnace 12 have independent temperature control and heating systems (not shown), respectively, the first furnace 11 and the second furnace 12 communicate with each other through the transition zone 13, and the quartz ampoule 2 includes glass raw materials The tube 21 and the purified glass tube 22, the glass raw material tube 21 and the purified glass tube 22 communicate with each other through the connecting tube 23, the glass raw material tube 21 is arranged in the first furnace 11, the purified glass tube 22 is arranged in the second furnace 12, and the connecting tube 23 is located in the transition zone 13.
Embodiment 2
[0013] Embodiment two: use the preparation device of embodiment one to prepare Ge 30 Sb 10 Se 60 Glass, the raw materials are 50 grams of germanium, antimony and selenium in proportions of 30mol%, 10mol% and 60mol% respectively, and 0.02 grams of magnesium bars are put into the glass raw material tube 21 at the same time according to the mass percentage of 0.04wt%, and the glass raw material is sealed The orifice of tube 21 is evacuated to 6 x 10 -4 Pa, seal the nozzle of the purified glass tube 22, put the vacuumed quartz ampoule 2 into the furnace, place the glass raw material tube 21 in the first furnace 11 for melting, and place the purified glass tube 22 in the second furnace 12. Raise the first furnace 11 to 250°C at a heating rate of 3°C / min, keep it warm for 2 hours, then raise it to 700°C at a heating rate of 3°C / min, keep it warm for 2 hours, and then heat it at a heating rate of 2°C / min The speed is raised to 1020°C, and kept at this temperature for 12 hours, so ...
Embodiment 3
[0014] Embodiment three: use the preparation device of embodiment one to prepare 80GeSe 2 -10Ga 2 Se 3 -10CsI glass, raw material according to GeSe 2 , Ga 2 Se 3 and CsI are respectively 80mol%, 10mol% and 10mol% proportioning 20 grams, simultaneously put 0.01 grams of magnesium bars according to mass percentage 0.05wt%, seal the nozzle of glass raw material pipe 21 after packing into glass raw material pipe 21, vacuumize up to 7×10 -4 Pa, seal the nozzle of the purified glass tube 22, put the vacuumed quartz ampoule 2 into the furnace, place the glass raw material tube 21 in the first furnace 11 for melting, and place the purified glass tube 22 in the second furnace 12. Raise the first furnace 11 to 250°C at a heating rate of 3°C / min, keep it warm for 2 hours, then raise it to 700°C at a heating rate of 2°C / min, keep it warm for 2 hours, and then heat it at a heating rate of 2°C / min Raise to 1000°C and keep it at this temperature for 12 hours, so that the swing furnace ...
PUM
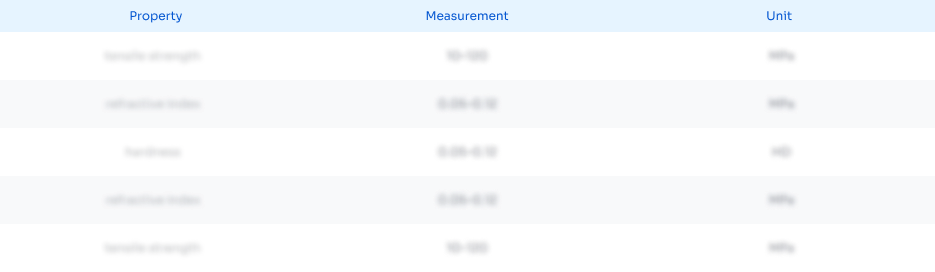
Abstract
Description
Claims
Application Information

- R&D
- Intellectual Property
- Life Sciences
- Materials
- Tech Scout
- Unparalleled Data Quality
- Higher Quality Content
- 60% Fewer Hallucinations
Browse by: Latest US Patents, China's latest patents, Technical Efficacy Thesaurus, Application Domain, Technology Topic, Popular Technical Reports.
© 2025 PatSnap. All rights reserved.Legal|Privacy policy|Modern Slavery Act Transparency Statement|Sitemap|About US| Contact US: help@patsnap.com