Wear resistant cast iron
A wear-resistant cast iron, weight percentage technology, applied in the field of cast iron, can solve the problems of great impact on wear resistance, insufficient hardness, corrosion resistance, high temperature oxidation resistance, and increased grinding and processing costs, etc., to achieve metallographic structure improvement, Broad prospects for economic benefits, the effect of improving hardness and wear resistance
- Summary
- Abstract
- Description
- Claims
- Application Information
AI Technical Summary
Problems solved by technology
Method used
Image
Examples
Embodiment 1
[0021] Embodiment 1: each ingredient is batched according to the following ratio: C: 2.8 (weight percent, the same below), Si: 0.2, Mn: 0.5, S: 0.01, P: 0.01, Cr: 21, Mo: 1.0, all the other are Fe and unavoidable impurities. After smelting, casting, annealing, quenching, tempering, cooling and storage, after testing, the Rockwell hardness HRc of the village material after treatment is 61.
Embodiment 2
[0022] Embodiment 2: each ingredient is batched according to the following ratio: C: 2.8 (weight percent, the same below), Si: 1, Mn: 1, S: 0.06, P: 0.1, Cr: 23, Ni: 1.5, Mo: 1.5 , and the rest are Fe and unavoidable impurities. After smelting, casting, annealing, quenching, tempering, cooling and warehousing, it is tested that the Rockwell hardness HRc of the material after treatment is 63.
Embodiment 3
[0023] Embodiment 3: each ingredient is batched according to the following ratio: C: 2.8 (weight percent, the same below), Si: 0.6, Mn: 0.75, S: 0.03, P: 0.05, Cr: 22, Ni: 0.5, Mo: 1.25 , and the rest are Fe and unavoidable impurities. After smelting, casting, annealing, quenching, tempering, cooling and warehousing, after testing, the Rockwell hardness HRc of the village material after treatment is 62.
PUM
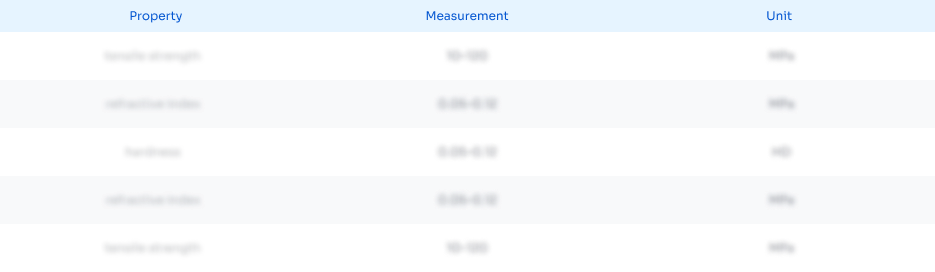
Abstract
Description
Claims
Application Information

- R&D
- Intellectual Property
- Life Sciences
- Materials
- Tech Scout
- Unparalleled Data Quality
- Higher Quality Content
- 60% Fewer Hallucinations
Browse by: Latest US Patents, China's latest patents, Technical Efficacy Thesaurus, Application Domain, Technology Topic, Popular Technical Reports.
© 2025 PatSnap. All rights reserved.Legal|Privacy policy|Modern Slavery Act Transparency Statement|Sitemap|About US| Contact US: help@patsnap.com