Smelting method of low-phosphorus steel
A technology of molten steel smelting and molten steel, which is applied in the field of low-phosphorus steel production, can solve the problems of reducing the age of the converter, occupying a long time of the converter, damage to the lining of the converter, etc., and achieve the effects of shortening the smelting period of the converter, less erosion and less slag
- Summary
- Abstract
- Description
- Claims
- Application Information
AI Technical Summary
Problems solved by technology
Method used
Examples
Embodiment 1
[0019] Take the deep dephosphorization of 500kg induction furnace as an example.
[0020] Melt 500kg of molten steel in an intermediate frequency induction furnace, ω[P]=0.0070%, and the temperature of molten steel is 1678°C. Metallurgical lime, red iron oxide, and bauxite are used as slagging agents and deep dephosphorizing agents. The total amount of slag added is 2.5 kg, its composition is 35% CaO, 30% FeO, 13% Fe 2 o 3 , 18% Al 2 o 3 , 2% SiO2, 1% MnO, 1% MgO. Use induction current to stir, after 5 minutes of treatment, tilt the crucible, scrape out the steel slag from the crucible, after scraping out more than 95%, add 1kg of metallurgical lime to make new slag, cover molten steel, molten steel ω[P] from 0.0070% to 0.0015 %.
Embodiment 2
[0022] Take the 180-ton converter application as an example.
[0023] ω[P]=0.04% into the molten iron in the converter. In the converter smelting, metallurgical lime, iron balls and light-burned dolomite are used as the slagging agent. The slagging amount is 8.9 tons, the smelting time is 30 minutes, and the tapping amount is 190 tons. Converter molten steel ω[P]=0.008%, add 0.8 tons of deep dephosphorization agent to the ladle, and then add 1.6 tons of deep dephosphorization agent after tapping. The composition of the dephosphorization agent is: 33% CaO, 29% FeO, 13 %Fe 2 o 3 , 18% Al 2 o 3 , 3% SiO2, 2% MnO, 2% MgO. The temperature of the molten steel is 1675°C, argon bottom blowing and stirring is carried out, and the gas supply intensity is 20Nm 3 / min, stirring time 5min. Then carry out the slag removal treatment, remove more than 95% of the steel slag in the ladle, and re-slag, that is, complete the dephosphorization treatment, and the molten steel ω[P]=0.004%. Co...
PUM
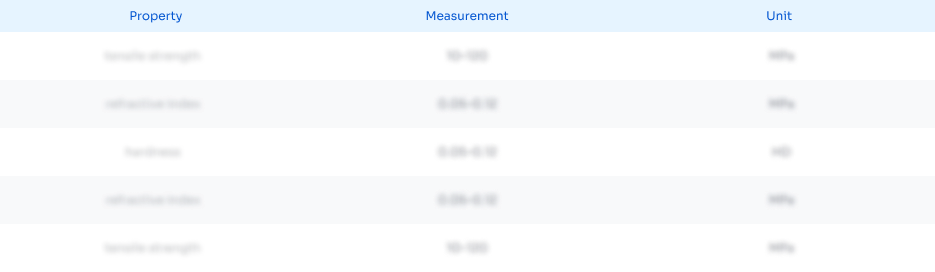
Abstract
Description
Claims
Application Information

- R&D
- Intellectual Property
- Life Sciences
- Materials
- Tech Scout
- Unparalleled Data Quality
- Higher Quality Content
- 60% Fewer Hallucinations
Browse by: Latest US Patents, China's latest patents, Technical Efficacy Thesaurus, Application Domain, Technology Topic, Popular Technical Reports.
© 2025 PatSnap. All rights reserved.Legal|Privacy policy|Modern Slavery Act Transparency Statement|Sitemap|About US| Contact US: help@patsnap.com