Aluminum silicon carbide and silicon carbide composite material and preparation method thereof
A technology of aluminum silicide and composite materials, applied in the field of composite refractory materials, can solve the problems of high cost and difficult industrialization, and achieve the effects of excellent performance, prolonged service life, and abundant raw material resources.
- Summary
- Abstract
- Description
- Claims
- Application Information
AI Technical Summary
Problems solved by technology
Method used
Examples
Embodiment 1
[0012] A kind of aluminum carbon silicide and silicon carbide composite material and its preparation method, first mix 35-40wt% of clay, 30-35wt% of industrial carbon powder and 30-35wt% of metal aluminum powder, and add 5-8wt% of the above mixture Calcium lignosulfonate, calcium lignosulfonate is first dissolved into an aqueous solution and then used as ingredients, stirred for 5-15 minutes, pressed into shape, dried at 90-110°C for 12-24 hours; then in an argon atmosphere and sintering under the condition of 1600-1700° C. for 5-6 hours, and cooling naturally to prepare aluminum carbide silicon carbide and silicon carbide composite materials.
[0013] The content and particle size of the mixture in this embodiment 1 are: the SiO of clay 2 Al content ≥ 40wt%, particle size 0.1-0mm; metal aluminum powder Al content ≥ 90wt%, particle size 0.1-0mm; industrial carbon powder C content ≥ 80wt%, particle size 0.1-0mm.
Embodiment 2
[0015] An aluminum carbon silicide and silicon carbide composite material and a preparation method thereof. First mix 40-45wt% clay, 20-25wt% industrial carbon powder and 30-35wt% metal aluminum powder, add 6-7wt% sodium lignosulfonate of the above mixture, and dissolve the sodium lignosulfonate first The aqueous solution is then used for batching, stirred for 10-15 minutes, pressed into shape, dried at 80-110°C for 18-30 hours; then sintered under argon atmosphere and at 1700-1800°C for 3-4 hours , Aluminum carbide silicon carbide and silicon carbide composite materials were obtained after natural cooling.
[0016] The content and particle size of the mixture in this embodiment 2 are the same as in embodiment 1.
Embodiment 3
[0018] A composite material of aluminum carbon silicide and silicon carbide and its preparation method: first mix 45-50 wt% of clay, 20-25 wt% of industrial carbon powder and 25-30 wt% of metal aluminum powder, and add 3-6 wt% of the above mixture Sulfurous acid pulp waste liquid, stirred for 5-15 minutes, pressed into shape, dried at 60-90°C for 24-36 hours; then sintered under argon atmosphere and at 1750-1800°C for 2-3 hours , Aluminum carbide silicon carbide and silicon carbide composite materials were obtained after natural cooling.
[0019] The content and the particle size of the mixture in the present embodiment 3 are the same as in the embodiment 1.
PUM
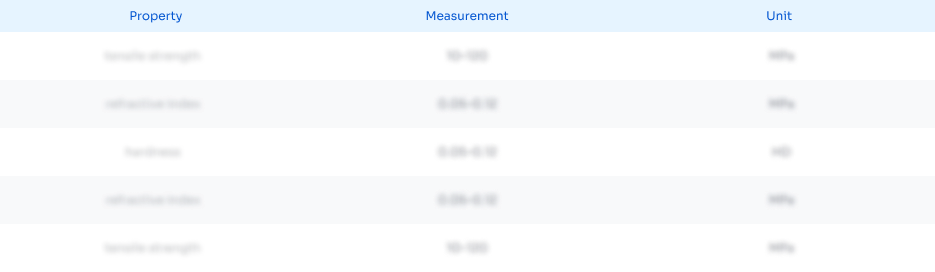
Abstract
Description
Claims
Application Information

- R&D
- Intellectual Property
- Life Sciences
- Materials
- Tech Scout
- Unparalleled Data Quality
- Higher Quality Content
- 60% Fewer Hallucinations
Browse by: Latest US Patents, China's latest patents, Technical Efficacy Thesaurus, Application Domain, Technology Topic, Popular Technical Reports.
© 2025 PatSnap. All rights reserved.Legal|Privacy policy|Modern Slavery Act Transparency Statement|Sitemap|About US| Contact US: help@patsnap.com