Method for preparing high molecule emulsifying agent for ASA
A polymer emulsifier and initiator technology, applied in the field of polymer chemistry, can solve the problems of easy demulsification of emulsions, adverse effects of sizing effects, slippage of paper sheets, etc.
- Summary
- Abstract
- Description
- Claims
- Application Information
AI Technical Summary
Problems solved by technology
Method used
Examples
Embodiment 1
[0007] Example 1: Mix polyvinyl alcohol and deionized water evenly at a mass ratio of 1:10, heat to 100°C, keep warm for 1 hour to completely dissolve the polyvinyl alcohol in the reactor, then cool down to 80°C to prepare polyvinyl alcohol Aqueous solution A; mix styrene, butyl acrylate, methacryloyloxyethyltrimethylammonium chloride, and acrylamide at a mass ratio of 1:1:0.2:1, oil-soluble vinyl monomer styrene and Mix butyl acrylate to obtain solution B, and mix cationic monomer methacryloyloxyethyltrimethylammonium chloride and hydrophilic vinyl monomer acrylamide to obtain solution C; mix deionized water and ammonium persulfate by 1: The mass ratio of 0.2 is uniformly mixed to obtain the ammonium persulfate aqueous solution D. Add 1 / 10 of the solution B, C and 1 / 2 of the initiator aqueous solution D to the solution A dropwise, and keep warm at 80°C for 0.7h to obtain the cationic soap-free styrene-acrylic polymer seed emulsion E. Then add the remaining solutions B, C and...
Embodiment 2
[0008] Example 2: Add polyvinyl alcohol and deionized water into a drying reactor at a mass ratio of 1:10, heat to 90°C, keep warm for 2 hours to completely dissolve the polyvinyl alcohol in the reactor, then cool down to 85°C to prepare To obtain polyvinyl alcohol aqueous solution A; methyl methacrylate, butyl acrylate, methacryloyloxyethyl dimethyl benzyl ammonium chloride, and acrylamide were mixed respectively in a mass ratio of 1:3:2:2, The oil-soluble vinyl monomer methyl methacrylate and butyl acrylate are mixed to obtain solution B, and the cationic monomer methacryloyloxyethyl dimethyl benzyl ammonium chloride and the hydrophilic vinyl monomer acrylamide are mixed to obtain Solution C: Mix deionized water and ammonium persulfate at a mass ratio of 1:0.3 to obtain initiator aqueous solution D. Add 1 / 10 of solutions B, C and 1 / 2 initiator aqueous solution D to solution A dropwise, keep warm and react for 0.5h to obtain cationic soap-free styrene-acrylic polymer seed emu...
Embodiment 3
[0009] Example 3: Add polyvinyl alcohol and deionized water into a drying reactor at a mass ratio of 1:10, heat to 95°C, keep warm for 2 hours to completely dissolve the polyvinyl alcohol in the reactor, and then cool down to 80°C to prepare To obtain polyvinyl alcohol aqueous solution A; methyl styrene, ethyl acrylate, methacryloyloxyethyl trimethyl ammonium chloride, and methylol acrylamide were mixed in a mass ratio of 1:5:3:5, The oil-soluble vinyl monomer methyl styrene and ethyl acrylate are mixed to obtain solution B, and the cationic monomer methacryloyloxyethyltrimethylammonium chloride and the hydrophilic vinyl monomer methylolacrylamide are mixed to obtain Solution C: Mix deionized water and ammonium persulfate-sodium bisulfite uniformly at a mass ratio of 1:0.6 to obtain aqueous initiator solution D. Add 1 / 10 of solutions B, C and 1 / 2 initiator aqueous solution D to solution A dropwise, keep warm and react for 1 hour to obtain cationic soap-free styrene-acrylic pol...
PUM
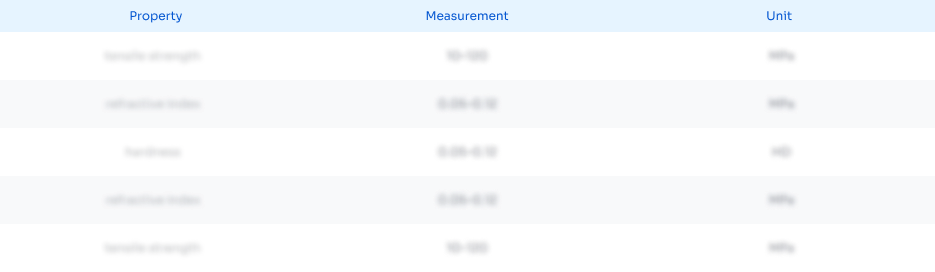
Abstract
Description
Claims
Application Information

- R&D
- Intellectual Property
- Life Sciences
- Materials
- Tech Scout
- Unparalleled Data Quality
- Higher Quality Content
- 60% Fewer Hallucinations
Browse by: Latest US Patents, China's latest patents, Technical Efficacy Thesaurus, Application Domain, Technology Topic, Popular Technical Reports.
© 2025 PatSnap. All rights reserved.Legal|Privacy policy|Modern Slavery Act Transparency Statement|Sitemap|About US| Contact US: help@patsnap.com