Method for jointly producing ferronickel in tunnel furnace-blast furnace from lateritic nickel
A laterite nickel ore and tunnel kiln technology, applied in chemical instruments and methods, solid separation, magnetic separation, etc., can solve problems such as increased cost of smelting ferronickel, increased acid consumption, and short process flow, achieving significant economic benefits and Social benefit, easy temperature control, and simple production process
- Summary
- Abstract
- Description
- Claims
- Application Information
AI Technical Summary
Problems solved by technology
Method used
Image
Examples
Embodiment 1
[0011] 1. The chemical composition of laterite nickel ore raw materials is as follows; Ni 0.8-1.2% Mg 12.1-18.3% Fe 8.34-11.2% Ai 0.04-0.06% Si 18-24%
[0012] 2. Process conditions: Crush 10 kg of laterite nickel ore with a particle size of 0-3 mm, add calcium chloride or magnesium chloride 5% of the raw material weight, mix evenly, put it into an extrusion machine to form a rough billet, and put it into a reduction tank , then add 3KG of the above-mentioned reducing agent, fill in the gap in the reduction tank, and cover it. Put it into a tunnel kiln at a temperature of 1000-1300 ℃, keep the temperature constant for 5 hours, after reduction, pulverize, magnetically separate, and then press the magnetically separated material into balls for drying, and then enter the blast furnace for smelting to obtain high-grade nickel-iron alloy, nickel grade It reached 17.2%, and the nickel recovery rate reached 87.16%.
Embodiment 2
[0014] A. The chemical composition of laterite nickel ore is as follows: Ni 1.01-1.2% Mg 13.2-16.3% Fe 10.34-13.25% Ai 0.051-0.06% Si 13.2-16.7%
[0015] B. Process conditions: take lateritic nickel ore and crush it to 10 kg, with a particle size of 0-3mm, add 7% of the original ore weight of calcium chloride or magnesium chloride and mix evenly, put it into an extruder to form a rough billet, and put it into a reduction Then add 2.5KG of the above-mentioned reducing agent into the tank, fill in the gap of the reduction tank and cover it. After being placed in the tunnel kiln at a temperature of 1000-1300°C and kept at a constant temperature for 6 hours, the reduced laterite nickel ore is crushed and magnetically separated, and then the magnetically separated material is pressed into balls, dried, and put into a blast furnace to obtain high-grade nickel. The ore alloy has a nickel grade of 16.4% and a nickel recovery rate of 86.23%.
Embodiment 3
[0017] A. The chemical composition of laterite nickel ore is as follows: Ni 0.92-1.31% Mg 15.3-19.4% Fe 2.01-23.4% Ai 3.2-4.81% Si 12.1-15.3%
[0018] B. Process conditions: Take 10 kg of laterite nickel ore and crush it to a particle size of 0-3mm, add 8% of the original ore weight calcium chloride or magnesium chloride and mix evenly, put it into an extruder to form it, make a rough billet, put it into the reduction In the tank, add 2KG of the above-mentioned carbonaceous reducing agent, fill in the gap in the reducing tank, and add a cover. Put it into a tunnel kiln, keep the temperature at 1000-1300°C for 7 hours, crush the reduced laterite nickel ore, and magnetically separate it, then press the magnetically separated reduced material into balls, dry it, and enter it into a blast furnace for smelting to obtain high-grade nickel ore. The nickel-iron alloy has a grade of 18.3%, and the recovery rate of nickel is 85.96%.
PUM
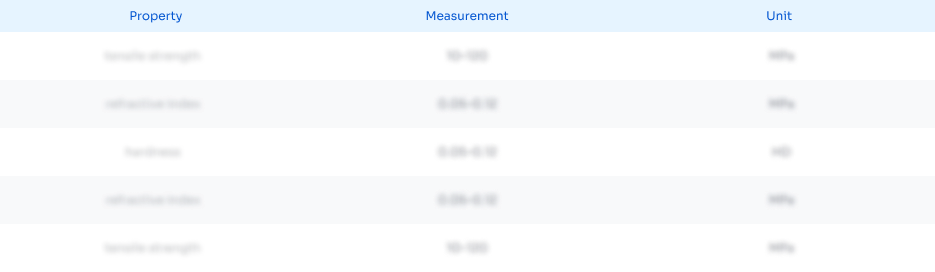
Abstract
Description
Claims
Application Information

- R&D Engineer
- R&D Manager
- IP Professional
- Industry Leading Data Capabilities
- Powerful AI technology
- Patent DNA Extraction
Browse by: Latest US Patents, China's latest patents, Technical Efficacy Thesaurus, Application Domain, Technology Topic, Popular Technical Reports.
© 2024 PatSnap. All rights reserved.Legal|Privacy policy|Modern Slavery Act Transparency Statement|Sitemap|About US| Contact US: help@patsnap.com