Fluid distributing valve, distributing valve combination unit and distributing system using the distributing valve
A fluid distribution valve and valve body technology, applied in distribution devices, engine components, engine lubrication, etc., can solve problems such as waste of lubricating oil, pollution of the working environment, insufficient pressure, etc., to avoid normal failures, and strong adaptability to impurities. , Set the effect of simple structure
- Summary
- Abstract
- Description
- Claims
- Application Information
AI Technical Summary
Problems solved by technology
Method used
Image
Examples
Embodiment 1
[0048] As shown in Figures 1 and 2, the fluid distributing valve of this embodiment includes a valve body 3, which is provided with a rotatable valve core 1 connected to an external drive device 41 through a transmission member 4, and a transmission member 4 Set on the right end of the valve core 1, the left end of the valve core 1 is closed in the valve body 3 by the end cover 7. The spool 1 is provided with a cavity, and the valve body 3 is also provided with an oil inlet valve body channel 29 and an oil outlet valve body channel 40 respectively opened on the surface of the valve body 3, and the cavity of the spool 1 is also slidably and sealingly connected with The cavity is divided into two parts, the first cavity 12 and the second cavity 11; the second cavity 11 is selectively connected to the oil outlet valve body channel 40 or the oil inlet valve body channel through the second valve core channel 13 29. Opposite to the communication direction of the second cavity 11 , ...
Embodiment 2
[0056]As shown in Figure 7, the difference between this embodiment and Embodiment 1 is that the plunger stroke detection device is an indicator rod 15 with one end fixedly connected to the plunger 2 and the other end protruding from the end cap 7, and an indicator rod 15 arranged on the valve body. 3 outer travel switches 16. A travel switch 16 is set at the left extreme position of the left end of the indicating rod 15 .
[0057] When the plunger 2 moves leftward or rightward with the indicating rod 15 and reaches the limit position, the operator can confirm the stroke position of the plunger 2 by observing the movement position of the indicating rod 15 . Of course, when the indicator rod 15 reaches the left limit position, it presses and triggers the travel switch 16 and makes it output the travel signal of the plunger 2 to the control system.
Embodiment 3
[0059] As shown in Figure 8 and Figure 9, the difference between this embodiment and Embodiment 1 is that there is no first spool channel 14 communicating with the first cavity 12, and a reset element is arranged in the first cavity 12 , The return element is a return spring 19, one end of the return spring 19 is press fit with the left end face of the plunger 2 and the other end is press fit with the end cap 7. Of course, the press fit between the above-mentioned spring 19 and the end cap 7 and the left end surface of the plunger 2 can also be a fixed connection. Due to the use of the spring 2, the fluid distribution valve of this embodiment has special requirements when in use, that is, the oil (fat) pressure at the oil inlet 9 of the valve body is greater than that formed by the elastic force of the spring 19 on the cross section of the plunger 2. The pressure formed by the elastic force of the spring 19 on the cross-section of the plunger 2 is greater than the back pressur...
PUM
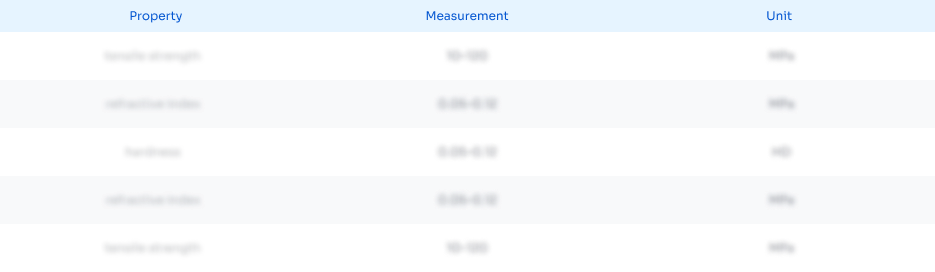
Abstract
Description
Claims
Application Information

- R&D
- Intellectual Property
- Life Sciences
- Materials
- Tech Scout
- Unparalleled Data Quality
- Higher Quality Content
- 60% Fewer Hallucinations
Browse by: Latest US Patents, China's latest patents, Technical Efficacy Thesaurus, Application Domain, Technology Topic, Popular Technical Reports.
© 2025 PatSnap. All rights reserved.Legal|Privacy policy|Modern Slavery Act Transparency Statement|Sitemap|About US| Contact US: help@patsnap.com