Method for producing ultra-coating dry abrasive paper
A production method and super-coating technology, applied in the field of polishing sandpaper and surface paint surface polishing, can solve the problems of easy clogging of sandpaper, loss of use performance, and reduced service life, etc., and achieve high strength, prolong service life, and not easy to clog Effect
- Summary
- Abstract
- Description
- Claims
- Application Information
AI Technical Summary
Problems solved by technology
Method used
Image
Examples
Embodiment approach 1
[0017] Embodiment 1: Use the latex paper produced by the French company ARJOWIGGINS as the substrate 1, and coat the substrate 1 with epoxy resin as the primer 2; then plant sand on the primer 2, and plant sand on the primer 2. Brown corundum abrasive 3 that has been calcined at high temperature; compound glue 4 is coated with phenolic resin binder mixed with nano-scale titanium dioxide after sand planting, and further wraps abrasive 3 to prevent it from falling off prematurely and affecting product grinding Lifespan; after regluing, rewind the sandpaper, and then cure the sandpaper, the curing temperature is 115°C, and the curing time is 8 hours; after curing, the sandpaper is flexed and humidified, and the assimilated sandpaper is sprayed with alcohol on the back to humidify Solution, the wetting solution is the aqueous solution that accounts for 10% by weight glycerin as hygroscopic agent and the polyethylene glycol that accounts for 0.5% as plasticizer, to ensure that sandp...
Embodiment approach 2
[0020] Embodiment 2: Use the latex paper produced by ARJOWIGGINS company in France as the substrate 1, and coat the polyurethane resin on the substrate 1 as the primer 2; then plant sand on the primer 2, and the sand planting is on the primer 2 Plant the brown corundum abrasive 3 that has been calcined at high temperature; the reglue 4 is to coat the phenolic resin binder mixed with nano-scale titanium dioxide and potassium fluoroborate after sand planting, and further wrap the abrasive 3 to prevent it from falling off prematurely It affects the grinding life of the product; after regluing, the sandpaper is rolled up, and then the sandpaper is cured, the curing temperature is 120 ° C, and the curing time is 6 hours; after curing, the sandpaper is flexed and humidified, and the back of the cured sandpaper Spray wine humidifying solution, humidifying solution is the aqueous solution that accounts for 15% by weight glycerin as hygroscopic agent and the polyethylene glycol that acc...
Embodiment approach 3
[0023] Embodiment 3: Use the latex paper produced by ARJOWIGGINS company in France as the substrate 1, and coat the polyurethane resin on the substrate 1 as the primer 2; then plant sand on the primer 2, and the sand planting is on the primer 2 Plant the brown corundum abrasive 3 that has been calcined at high temperature; the reglue 4 is to coat the phenolic resin binder mixed with nano-scale titanium dioxide, potassium fluoroborate, and sodium hexafluoroaluminate after sand planting, and further wrap the abrasive 3, so that It avoids premature falling off and affects the grinding life of the product; after regluing, the sandpaper is rolled up, and then the sandpaper is cured, the curing temperature is 125°C, and the curing time is 3 hours; after curing, the sandpaper is flexed and humidified, The backside of the solidified sandpaper is sprayed with a wetting solution, and the wetting solution is an aqueous solution of 25% by weight of glycerin as a hygroscopic agent and 2% of...
PUM
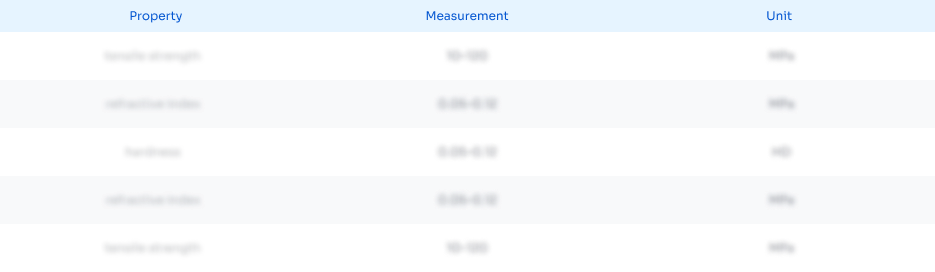
Abstract
Description
Claims
Application Information

- R&D Engineer
- R&D Manager
- IP Professional
- Industry Leading Data Capabilities
- Powerful AI technology
- Patent DNA Extraction
Browse by: Latest US Patents, China's latest patents, Technical Efficacy Thesaurus, Application Domain, Technology Topic, Popular Technical Reports.
© 2024 PatSnap. All rights reserved.Legal|Privacy policy|Modern Slavery Act Transparency Statement|Sitemap|About US| Contact US: help@patsnap.com