New catalystic reactor method for producing commercial grade pulp, native lignin and single cell protein
A catalytic reaction, lignin technology, applied in pulp dehydration, pulp by-product recovery, pulping with inorganic alkali, etc., to achieve high yield, high efficiency, and high pulp yield.
- Summary
- Abstract
- Description
- Claims
- Application Information
AI Technical Summary
Problems solved by technology
Method used
Image
Examples
Embodiment Construction
[0041] figure 1 A schematic diagram of a preferred embodiment of the method of the invention is shown. The wood chips from the feed port 2 are placed in the impregnation chamber 4 together with the impregnation liquid. After allowing the chips to soak for an appropriate time, excess impregnating liquid is removed and washed, such as by filter mechanism 6; and collected in recovery tank 10. Afterwards, it is enriched and returned to the impregnation chamber 4 , for example by means of a pump 12 . At the same time, the impregnated wood chips are transported to the catalytic reactor 20 by appropriate means, such as the screw conveying mechanism 8 . To control the delivery of wood chips from the impregnation chamber 4 to the catalytic reactor 20, various mechanisms can be used. In a preferred embodiment, storage tank 14 holds the impregnated wood chips until they can be conveyed via funnel 16 into measurement device 18 . Measuring device 18 controls the feed rate of wood chips...
PUM
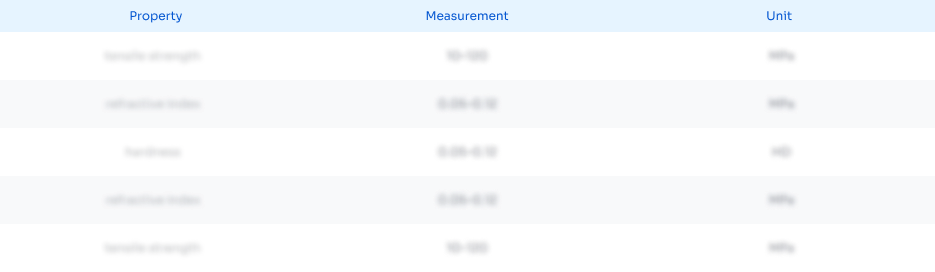
Abstract
Description
Claims
Application Information

- R&D
- Intellectual Property
- Life Sciences
- Materials
- Tech Scout
- Unparalleled Data Quality
- Higher Quality Content
- 60% Fewer Hallucinations
Browse by: Latest US Patents, China's latest patents, Technical Efficacy Thesaurus, Application Domain, Technology Topic, Popular Technical Reports.
© 2025 PatSnap. All rights reserved.Legal|Privacy policy|Modern Slavery Act Transparency Statement|Sitemap|About US| Contact US: help@patsnap.com