Method for preparing polydiallyl itaconate and dimer acid
A technology of dimer acid methyl ester and fatty acid methyl ester, which is applied in the field of mixed unsaturated fatty acid methyl ester, can solve the problems affecting the yield and quality of dimer acid methyl ester, increase the difficulty of separation, oxidation reaction, etc., and achieve the goal of equipment The effect of reduced requirements, simple method and fast separation speed
- Summary
- Abstract
- Description
- Claims
- Application Information
AI Technical Summary
Problems solved by technology
Method used
Examples
Embodiment 1
[0024] Embodiment 1: in 0.5L reactor, add rapeseed oil fatty acid methyl ester (main component is methyl oleate, methyl linoleate, methyl linolenate, acid value 1.58mgKOH / g oil), cocatalyst thick The amount of sulfuric acid added is 0.15%, and mechanically stirred at about 50-55°C for about 1 hour. Then add 3.5% anhydrous aluminum trichloride, and rapidly heat up to about 170 ℃ for polymerization reaction, the polymerization reaction ends (5 hours), the reaction mixture is added the dilute solution (pH=7.5) of weak base sodium carbonate, sedimentation 10 hours (or direct centrifugation), separate the lower layer of aluminum hydroxide and a small amount of impurities, the upper layer is thick dimer acid methyl ester (iodine value 67), after warm water washing treatment to neutrality, the thick dimer acid methyl ester is obtained, The yield was 83.0%.
[0025] Gained thick dimer acid methyl ester enters molecular distillation device, and condition is vacuum tightness 4-10Pa, di...
Embodiment 2
[0026] Embodiment 2: in 0.5L reactor, add safflower seed oil fatty acid methyl ester (main component is methyl oleate, methyl linoleate, methyl linolenate, acid value 2.38mgKOH / g oil), cocatalyst The added amount of concentrated sulfuric acid is 0.2%, and mechanically stirred at about 50-55°C for about 1.5 hours. Then add 4.5% anhydrous zinc trichloride, and rapidly heat up to about 200°C for polymerization reaction, the polymerization reaction ends (6 hours), the reaction mixture is added a dilute solution of weak alkali sodium carbonate (pH=7.5), and settles for 10 hours (or direct centrifugation), separate the lower layer of zinc hydroxide and a small amount of impurities, the upper layer is thick dimer acid methyl ester (iodine value 66), after warm water washing treatment to neutrality, the thick dimer acid methyl ester is obtained, producing The rate is 85.0%.
[0027] Gained thick dimer acid methyl ester enters molecular distillation device, and condition is vacuum tig...
Embodiment 3
[0028] Embodiment 3: in 0.5L reactor, add mixed unsaturated fatty acid methyl ester (the total content of oleic acid methyl ester, linoleic acid methyl ester, linolenic acid methyl ester is 92%, acid value 0.75mgKOH / g oil), Concentrated sulfuric acid as a cocatalyst is added in an amount of 0.2%, and mechanically stirred at about 50-55°C for about 0.5 hours. Then add 4.0% anhydrous aluminum trichloride, and rapidly heat up to about 190°C for polymerization reaction, the polymerization reaction ends (5 hours), the reaction mixture is added a dilute solution of weak alkali sodium carbonate (pH=7.5), and settles for 10 hours (or direct centrifugation), separate the lower layer of zinc hydroxide and a small amount of impurities, the upper layer is thick dimer acid methyl ester (iodine value 65), after warm water washing and processing to neutrality, the thick dimer acid methyl ester is obtained, producing The rate is 85.2%.
[0029] Gained thick dimer acid methyl ester enters mol...
PUM
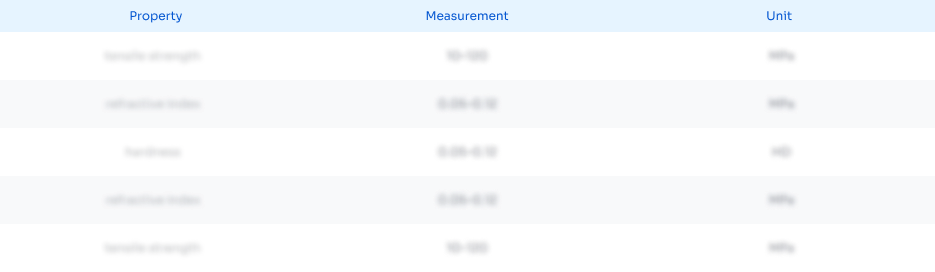
Abstract
Description
Claims
Application Information

- R&D
- Intellectual Property
- Life Sciences
- Materials
- Tech Scout
- Unparalleled Data Quality
- Higher Quality Content
- 60% Fewer Hallucinations
Browse by: Latest US Patents, China's latest patents, Technical Efficacy Thesaurus, Application Domain, Technology Topic, Popular Technical Reports.
© 2025 PatSnap. All rights reserved.Legal|Privacy policy|Modern Slavery Act Transparency Statement|Sitemap|About US| Contact US: help@patsnap.com