Process for synthesizing core-shell structure compound molecular sieve and use thereof
A technology of composite molecular sieve and core-shell structure, which is applied in the synthesis field of core-shell structure composite molecular sieve, and can solve the problems of large particle diameter and inability to form core-shell structure composite molecular sieve, etc.
- Summary
- Abstract
- Description
- Claims
- Application Information
AI Technical Summary
Problems solved by technology
Method used
Image
Examples
Embodiment 1
[0024] Example 1: Mix 5.0 g of phosphorus pentoxide with 15 ml of deionized water, and load it onto the surface of 10.0 g of HZSM-5 raw powder by dipping (self-made, with a silicon-aluminum ratio of 76), and treat it at 180 ° C for 48 hours. P-ZSM-5 with the phosphorus source immobilized on the surface of ZSM-5 was obtained. P-ZSM-5 was added to 3.5 g of pseudoboehmite (w(Al 2 O 3 )=68%), 6.2g silica sol (w(SiO 2 ) 40%)) and 10 g of deionized water, after stirring, add 1.46 g of triethylamine.
[0025] The above gel was put into an autoclave, formed at room temperature for 10 hours, firstly crystallized at 120 °C for 7 hours, and then crystallized at 170 °C for 48 hours. The solid obtained by filtration of the product was washed with water, and dried at 160° C. for 24 h to obtain sample C.
[0026] The X powder diffraction of sample C is shown in Figure 1, and the scanning electron microscope is shown in Figure 4.
Embodiment 2
[0029] Example 2: Mix 7.8g of ammonium hydrogen phosphate and ammonium dihydrogen phosphate mixture with 15ml of deionized water, and add to 25.5g of HZSM-5 powder by ion exchange (self-made, silicon-aluminum ratio is 76), 300 ℃ for 4 hours to prepare P-ZSM-5 with phosphorus source immobilized on the surface of ZSM-5. P-ZSM-5 was added to 5.9g pseudo-boehmite (w(Al 2 o 3 )=68%), 11.2g silica sol (w(SiO 2 )=40%)) and 10 g of deionized water, after stirring, 1.35 g of triethylamine was added.
[0030] The above gel was placed in an autoclave, aged at room temperature for 5 hours, then crystallized at a constant temperature of 120°C for 7 hours, and then crystallized at a constant temperature of 180°C for 48 hours. The product was washed by filtration and dried at 160°C for 24h. The X powder diffraction spectrum of the obtained sample has the characteristics of accompanying drawing 1.
Embodiment 3
[0031] Example 3: Load 11.5g of phosphorus powder on the surface of 34.2g of HZSM-5 raw powder (self-made, with a silicon-aluminum ratio of 76) by vapor deposition, and keep the temperature at 600°C for 2 hours to obtain a phosphorus source fixed on the surface of ZSM-5 The P-ZSM-5. P-ZSM-5 was added to 4.6g pseudo-boehmite (w(Al 2 o 3 )=68%), 5.3g of ethyl orthosilicate and 10g of deionized water mixture, after stirring, add 5.43g of triethylamine.
[0032] The above gel was put into an autoclave, and crystallized at a constant temperature of 80°C for 10h, and at a constant temperature of 200°C for 24h. The product was filtered and washed, and dried at 160°C for 24 hours to obtain sample D. The X powder diffraction spectrum of the obtained sample has the characteristics of accompanying drawing 1.
PUM
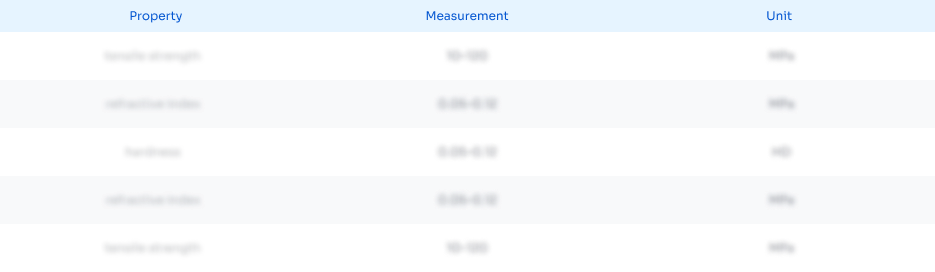
Abstract
Description
Claims
Application Information

- R&D Engineer
- R&D Manager
- IP Professional
- Industry Leading Data Capabilities
- Powerful AI technology
- Patent DNA Extraction
Browse by: Latest US Patents, China's latest patents, Technical Efficacy Thesaurus, Application Domain, Technology Topic, Popular Technical Reports.
© 2024 PatSnap. All rights reserved.Legal|Privacy policy|Modern Slavery Act Transparency Statement|Sitemap|About US| Contact US: help@patsnap.com