Anneal technique for producing SPCC steel grade with zincing wire annealing oven
An annealing process, an annealing furnace technology, applied in furnaces, heat treatment furnaces, manufacturing tools, etc., can solve problems such as galvanizing line shutdown or semi-stop production, continuous annealing furnace complex structure, substrate surface oxidation, etc., to reduce depreciation losses, eliminate The effect of increasing the production cycle and elongation rate
- Summary
- Abstract
- Description
- Claims
- Application Information
AI Technical Summary
Problems solved by technology
Method used
Image
Examples
Embodiment 1
[0028] Example 1: Variety SPCC, specification 1.0*1250mm, process: the operating speed of the production line is 53mpmin, after the strip steel is cleaned, the strip steel enters the furnace, and after being preheated to 170°C in the preheating section, the strip steel enters the direct combustion section Heated by an open flame to 624°C, the strip steel is heated to 740°C by the radiant tube heating section, the strip steel in the soaking section of the radiant tube is kept at 720°C by the electric radiant tube, and the strip steel is cooled to 200°C in the spray cooling section, and the furnace temperature is 140°C ℃. Protective gas: Nitrogen flow rate 701m 3 / hr, pressure 4.3bar, oxygen content 6.79ppm; hydrogen flow rate 65.6m 3 / hr, pressure 2.7bar, percentage 7.80%; gas pressure 83.1mdar; dew point of direct combustion section: -39.81°C, dew point of zone 1 of spray cooling section: -60°C.
Embodiment 2
[0029] Example 2: Variety SPCC, specification 1.5*1250mm, process: the operating speed of the production line is 38mpmin, after the strip steel is cleaned, the strip steel enters the furnace, and after being preheated to 140°C in the preheating section, the strip steel enters the direct combustion section The steel strip is heated to 610°C by an open flame, and the strip steel is heated to 764°C by the radiant tube heating section. The strip steel is kept at 690°C in the soaking section of the radiant tube, and is cooled to 230°C in the spray cooling section, and the furnace temperature is 180°C. Protective gas: nitrogen flow 500m 3 / hr, pressure 4.1bar, oxygen content 6.93ppm; hydrogen flow rate 65.5m 3 / hr, pressure 2.4bar, percentage 7.92%; gas pressure 96.5mdar; dew point of direct combustion section: -40°C, dew point of zone 1 of spray cooling section: -67°C.
Embodiment 3
[0030] Example 3: Variety SPCC, specification 0.5*1250mm, technological process: the operating speed of the production line is 76mpmin, after the strip steel is cleaned, the strip steel enters the furnace, and after being preheated to 180°C in the preheating section, the strip steel enters the direct combustion section The steel strip is heated to 630°C by the open flame, and the strip steel is heated to 790°C by the radiant tube heating section. The strip steel is kept at 730°C in the radiant tube soaking section, and the strip steel is cooled to 190°C in the spray cooling section, and the furnace temperature is 160°C. Protective gas: Nitrogen flow rate 701m 3 / hr, pressure 1.3bar, oxygen content 7ppm; hydrogen flow 90m 3 / hr, pressure 2.7bar, percentage 8.03%; gas pressure 83.1mdar; dew point of direct combustion section: -40°C, dew point of zone 1 of spray cooling section: -69°C.
PUM
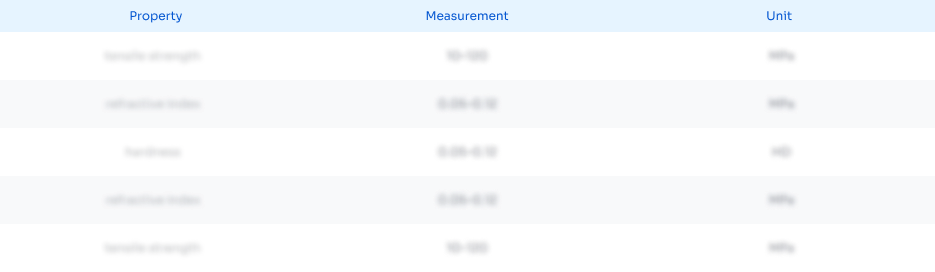
Abstract
Description
Claims
Application Information

- R&D
- Intellectual Property
- Life Sciences
- Materials
- Tech Scout
- Unparalleled Data Quality
- Higher Quality Content
- 60% Fewer Hallucinations
Browse by: Latest US Patents, China's latest patents, Technical Efficacy Thesaurus, Application Domain, Technology Topic, Popular Technical Reports.
© 2025 PatSnap. All rights reserved.Legal|Privacy policy|Modern Slavery Act Transparency Statement|Sitemap|About US| Contact US: help@patsnap.com