Distillation zinc smelting technique by using biomass charcoal as reducer
A biomass charcoal and reducing agent technology, applied in the field of non-ferrous metallurgy, can solve the problems of rising prices, increasing production costs, threatening the development of distillation zinc smelting process, etc., achieving the effect of high reduction efficiency and strong adaptability
- Summary
- Abstract
- Description
- Claims
- Application Information
AI Technical Summary
Problems solved by technology
Method used
Image
Examples
example 1
[0013] Example 1: Biomass charcoal is used as reducing agent ingredients to make dough, wherein the biomass charcoal is corn stalk charcoal. The main components of raw materials oxidized ore and corn stalk charcoal are as follows:
[0014]
[0015] According to the percentages of oxidized ore, corn stalk charcoal and binder, the ingredients are 58%, corn stalk charcoal 29%, and binder 13%. Mix the finely ground oxidized ore with corn stalk charcoal, grind it with a binder, and then make it into a wet agglomerate, and then dry the wet agglomerate to become a dry agglomerate with a moisture content of less than 2%. The ore is coked at 840-850°C for 20 minutes and then sent to the distillation furnace for distillation at 1040-1060°C. The reduction efficiency of distillation for 3 hours was 92.47%.
example 2
[0016] Example 2: Part of the biomass charcoal and part of the washed coal are used together as a reducing agent batching to make dough, wherein the biomass charcoal is corn stalk charcoal. The main components of raw materials oxidized ore, washed coal and corn stalk charcoal are as follows:
[0017]
[0018] According to the percentage of oxidized ore, corn stalk charcoal and binder, the ingredients are 58%, 15% corn stalk charcoal, 14.5% washed coal and 12.5% binder. Mix the finely ground oxidized ore, washed coal and corn stalk charcoal, grind them with binders, and then make wet agglomerates, and then dry the wet agglomerates to become dry agglomerates with a moisture content of less than 2%. The ore and dry agglomerated ore are coked at 840-850°C for 20 minutes and then sent to the distillation furnace for distillation at 1040-1060°C. The reduction efficiency of distillation for 3 hours was 91.72%.
PUM
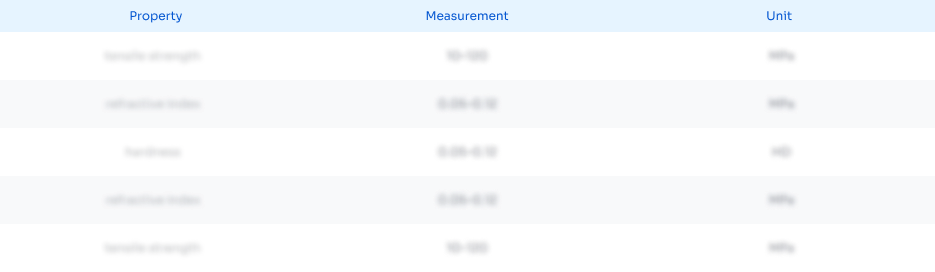
Abstract
Description
Claims
Application Information

- R&D
- Intellectual Property
- Life Sciences
- Materials
- Tech Scout
- Unparalleled Data Quality
- Higher Quality Content
- 60% Fewer Hallucinations
Browse by: Latest US Patents, China's latest patents, Technical Efficacy Thesaurus, Application Domain, Technology Topic, Popular Technical Reports.
© 2025 PatSnap. All rights reserved.Legal|Privacy policy|Modern Slavery Act Transparency Statement|Sitemap|About US| Contact US: help@patsnap.com