Method for deep-UV lithography making T type gate
A deep ultraviolet and deep ultraviolet technology, which is applied in the field of deep ultraviolet lithography to make "T" gates, can solve the problems of low processing efficiency and reduced gate length
- Summary
- Abstract
- Description
- Claims
- Application Information
AI Technical Summary
Problems solved by technology
Method used
Image
Examples
Embodiment Construction
[0026] The present invention is described in further detail below in conjunction with accompanying drawing:
[0027] Such as figure 1 As shown, the substrate 1 adopts a common cleaning method to make the substrate 1 clean and free from contamination, and the moisture on the surface of the substrate 1 is dried in a clean environment at 150 degrees Celsius to 180 degrees Celsius.
[0028] Such as figure 2 As shown, chemically amplified photoresist 2 for 248nm wavelength photolithography is coated on the substrate. The photoresist 2 has a resolution of 0.2 microns or more and a thickness of about 3000-5000 angstroms. UV135 photoresist is used at 90 degrees Celsius Bake for 60-90 seconds at -130 degrees Celsius.
[0029] Such as image 3 As shown, a deep ultraviolet (wavelength 248nm) exposure machine is used for alignment and exposure, and a suitable photoresist plate is selected according to the resolution performance of the lithography machine and the required gate length, ...
PUM
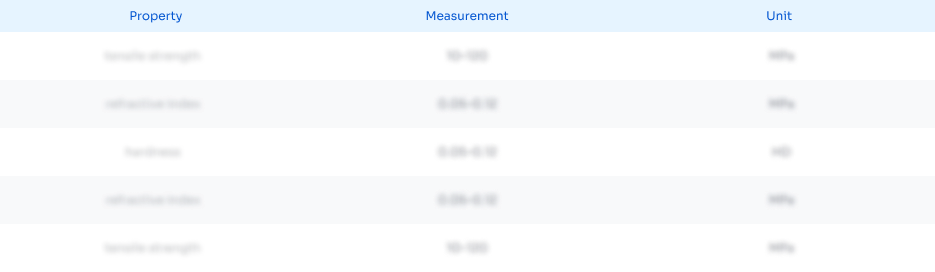
Abstract
Description
Claims
Application Information

- R&D Engineer
- R&D Manager
- IP Professional
- Industry Leading Data Capabilities
- Powerful AI technology
- Patent DNA Extraction
Browse by: Latest US Patents, China's latest patents, Technical Efficacy Thesaurus, Application Domain, Technology Topic, Popular Technical Reports.
© 2024 PatSnap. All rights reserved.Legal|Privacy policy|Modern Slavery Act Transparency Statement|Sitemap|About US| Contact US: help@patsnap.com