Exterior wall thermal insulation foaming putty
A technology of external wall insulation and putty, applied in the direction of filling slurry, etc., can solve problems such as poor adhesion, difficult construction, cracking, etc., and achieve good crack resistance and excellent thermal insulation effect
- Summary
- Abstract
- Description
- Claims
- Application Information
AI Technical Summary
Problems solved by technology
Method used
Examples
Embodiment 1
[0013] h 2 O25 kg, isothiazolinone 0.15 kg, acrylate 1.5 kg, dispersant 0.5 kg, ethylene glycol 1.5 kg, NH 4 HCO 3 2 kg, 2 kg of lauryl alcohol, 5 kg of polypropylene fiber, 0.6 kg of hydroxyethyl cellulose, 20 kg of styrene-acrylic latex, 30 kg of Caco3 powder, 40 kg of talcum powder, 5 kg of polyphenylene particles, 1.5 kg of wax emulsion kilogram.
Embodiment 2
[0015] h 2 15 kg of O, 0.05 kg of isothiazolinone, 0.8 kg of acrylate, 0.2 kg of dispersant, 1 kg of ethylene glycol, NH 4 HCO 3 0.5 kg, 1 kg of dodecyl alcohol, 3 kg of wood fiber or polypropylene fiber, 0.4 kg of hydroxyethyl cellulose, 10 kg of styrene-acrylic latex, 20 kg of Caco3 powder, 30 kg of talcum powder, 3 kg of polystyrene particles, Wax emulsion 0.5 kg.
Embodiment 3
[0017] h 2 O20 kg, 0.1 kg of isothiazolinone, 1.2 kg of acrylate, 0.35 kg of dispersant, 1.25 kg of propylene glycol, NH 4 HCO 3 1.3 kg, 1.5 kg of dodecyl alcohol, 4 kg of polypropylene fiber, 0.5 kg of hydroxyethyl cellulose, 15 kg of styrene-acrylic latex, 25 kg of Caco3 powder, 35 kg of talcum powder, 4 kg of polyphenylene particles, 1 wax emulsion kilogram.
[0018] As a preferred embodiment, the manufacturing process of the above-mentioned exterior wall foaming putty is as follows: first make the described H 2 O, preservatives, acrylates, dispersants, antifreeze, NH 4 HCO 3 , lauryl ester alcohol, wood fiber or polypropylene fiber, and water retaining agent are added in order under stirring, and stirred for about 55-65 minutes, preferably about 60 minutes, and then heated to 50-60°C with jacket steam , let the blowing agent (NH 4 HCO 3 ) slowly emits gas at a suitable temperature, thereby producing a large amount of smiling foams and generating foam slurry; the abo...
PUM
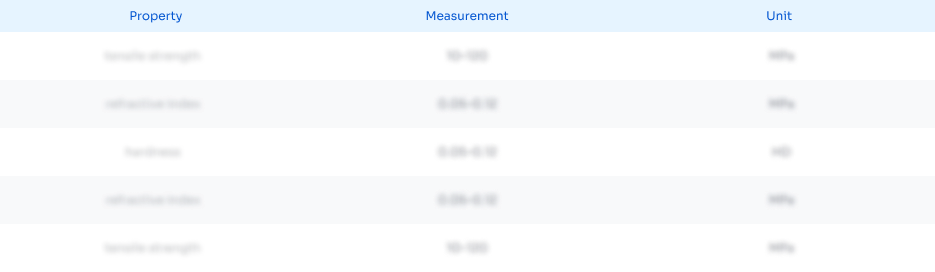
Abstract
Description
Claims
Application Information

- R&D Engineer
- R&D Manager
- IP Professional
- Industry Leading Data Capabilities
- Powerful AI technology
- Patent DNA Extraction
Browse by: Latest US Patents, China's latest patents, Technical Efficacy Thesaurus, Application Domain, Technology Topic, Popular Technical Reports.
© 2024 PatSnap. All rights reserved.Legal|Privacy policy|Modern Slavery Act Transparency Statement|Sitemap|About US| Contact US: help@patsnap.com