Method for making alumina ceramic core and core leach method
A kind of technology of alumina ceramics and production methods, applied in the direction of core, casting mold, casting mold composition, etc., can solve the problems of small opening porosity, cracking of ceramic core, long time for core removal, etc., and achieve good creep resistance at high temperature , Improve the effect of core removal speed
- Summary
- Abstract
- Description
- Claims
- Application Information
AI Technical Summary
Problems solved by technology
Method used
Image
Examples
Embodiment 1
[0028] Example 1: 75g of 180-mesh corundum powder, 265g of 250-mesh corundum powder and 290g of 325-mesh corundum powder were mixed with 150g of activated alumina and 30g of graphite powder by ball milling for 10 hours, and the ball-to-material ratio was 1:2.
[0029] Heat the plasticizer composed of 8g polyethylene, 22g beeswax and 160g paraffin to 60°C, gradually add it to the above-mentioned ball mixture, continue to stir and mix for 2 hours, and make alumina ceramic core plasticizer.
[0030] The above-mentioned plasticizer is pressed into a ceramic core according to the blade to be formed by hot pressing injection, and the hot pressing injection temperature is 50°C.
[0031] Fill the above-mentioned ceramic core in the sagger with alumina powder, and then pre-fire it; Heating to 1150°C, holding at 1150°C for 1 hour, and then cooling with the furnace.
[0032] The pre-fired ceramic core is taken out from the alumina powder for final firing. The final firing temperature is...
Embodiment 2
[0033] Example 2: 63g of 180-mesh corundum powder, 220g of 250-mesh corundum powder and 275g of 325-mesh corundum powder were mixed with 200g of activated alumina and 50g of graphite powder by ball milling for 20 hours, and the ball-to-material ratio was 1:2.
[0034] Heat the plasticizer composed of 10g polyethylene, 20g beeswax and 170g paraffin to 65°C, gradually add it to the above-mentioned ball mixture, continue stirring and mixing for 2.5 hours, and make alumina ceramic core plasticizer.
[0035] The above-mentioned plasticizer is pressed into a ceramic core according to the blade to be formed by hot pressing injection, and the hot pressing injection temperature is 55°C.
[0036] Fill the above ceramic core in the sagger with alumina powder, and then pre-fire; the pre-fire process is: rise from room temperature to 550°C within 5 hours, keep at 550°C for 4 hours, and then continue within 2.5 hours Heating to 1200°C, holding at 1200°C for 1.5 hours, and then cooling with ...
Embodiment 3
[0038] Example 3: 51 g of 180-mesh corundum powder, 255 g of 250-mesh corundum powder, 204 g of 325-mesh corundum powder, 300 g of activated alumina and 10 g of graphite powder were ball milled for 30 hours, and the ball-to-material ratio was 1:2.
[0039] Heat the plasticizer composed of 6g polyethylene, 27g beeswax and 147g paraffin to 70°C, gradually add it to the above-mentioned ball mixture, and continue to stir and mix for 3 hours to make alumina ceramic core plasticizer.
[0040] The above-mentioned plasticizer is pressed into a ceramic core according to the blade to be formed by hot pressing injection, and the hot pressing injection temperature is 60°C.
[0041] Use alumina powder to bury the above-mentioned ceramic core in a sagger, and then pre-fire; the pre-fire process is as follows: rise from room temperature to 600°C within 6 hours, keep at 600°C for 5 hours, and then continue within 3 hours Heat to 1100°C, hold at 1100°C for 2 hours, and then cool with the furna...
PUM
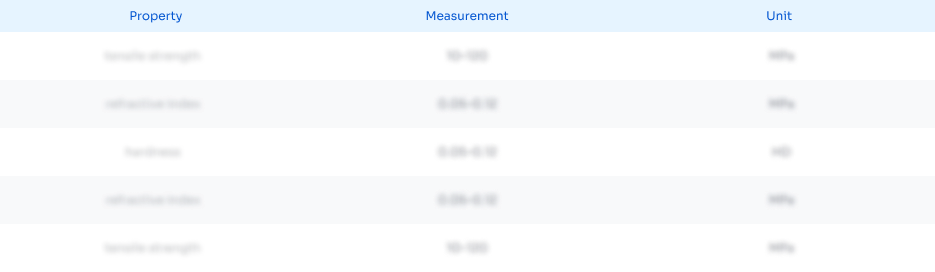
Abstract
Description
Claims
Application Information

- R&D
- Intellectual Property
- Life Sciences
- Materials
- Tech Scout
- Unparalleled Data Quality
- Higher Quality Content
- 60% Fewer Hallucinations
Browse by: Latest US Patents, China's latest patents, Technical Efficacy Thesaurus, Application Domain, Technology Topic, Popular Technical Reports.
© 2025 PatSnap. All rights reserved.Legal|Privacy policy|Modern Slavery Act Transparency Statement|Sitemap|About US| Contact US: help@patsnap.com