Shaped LED lampshade emitted/extruded using in-mold transfer thin membrane
A technology of light-emitting diodes and in-mold transfer, which is applied in lampshades, semiconductor devices of light-emitting elements, and processes for producing decorative surface effects, etc. The effect of improving the yield rate, reducing the cost, and mass production
- Summary
- Abstract
- Description
- Claims
- Application Information
AI Technical Summary
Problems solved by technology
Method used
Image
Examples
Embodiment Construction
[0023] Such as figure 1 As shown, the light-emitting diode lampshade that utilizes in-mold transfer printing film injection / extrusion molding of the present invention can quickly print an in-mold transfer printing film 10 mainly through output devices such as a printing machine or a printer, so that the mold The inner transfer printing film 10 is suitable for continuous plastic injection / extrusion molding and is integrally formed and combined with the lampshade of the light-emitting diode; the printing machine equipment can be a coating machine, a screen printing machine, a gravure printing machine or a relief printing machine, etc., the printer equipment can be laser color printer or inkjet color printer, etc.; 3 and an adhesive layer 4 to form an in-mold transfer film 10, wherein:
[0024] The transparent base layer 1 can be selected as PET (polyester resin), PMMA (polymethyl methacrylate resin), PC (polycarbonate resin), ABS (polyacrylonitrile-butadiene-styrene resin) or P...
PUM
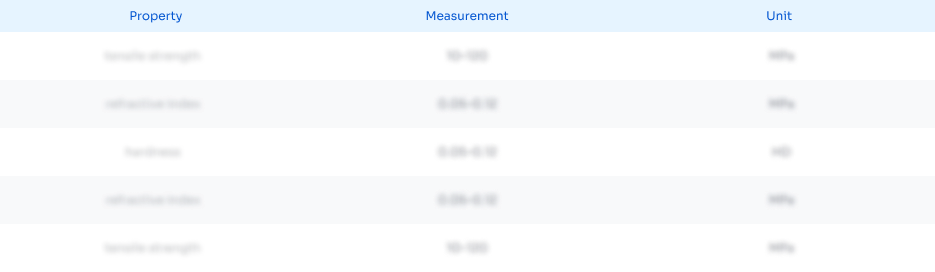
Abstract
Description
Claims
Application Information

- R&D
- Intellectual Property
- Life Sciences
- Materials
- Tech Scout
- Unparalleled Data Quality
- Higher Quality Content
- 60% Fewer Hallucinations
Browse by: Latest US Patents, China's latest patents, Technical Efficacy Thesaurus, Application Domain, Technology Topic, Popular Technical Reports.
© 2025 PatSnap. All rights reserved.Legal|Privacy policy|Modern Slavery Act Transparency Statement|Sitemap|About US| Contact US: help@patsnap.com