Non-chromium treatment fluid for preparation of corrosion-resistant oxidation film on magnesium alloy surface and method of use thereof
A corrosion-resistant, magnesium alloy technology, applied in the direction of metal material coating process, etc., can solve the problems of low film-forming efficiency, and achieve the effects of less environmental pollution, good adhesion, and long-term use of the solution
- Summary
- Abstract
- Description
- Claims
- Application Information
AI Technical Summary
Problems solved by technology
Method used
Image
Examples
Embodiment 1
[0028] After the solution of the present invention is prepared, it needs to be stirred rapidly under the air, so that the solution can fully react. During chemical conversion treatment, the micro-cathode and micro-anode on the surface of the magnesium alloy undergo an electrochemical reaction. Among them, there are micro-anodes and micro-cathodes on the surface of the magnesium alloy in the electrolyte, the anode: the α phase with a relatively negative potential, and the cathode: a metal with a relatively positive potential The second phase of the compound is the β phase. The electrochemical reaction of micro-cathode and micro-anode on the surface of the magnesium alloy leads to a local region with a higher pH value on the surface of the magnesium alloy sample, where hydroxide precipitates are deposited.
[0029] The reaction of conversion film formation on the surface of magnesium alloy can be expressed as follows:
[0030] Microanodic reaction on magnesium alloy surface:
...
Embodiment 2
[0063] The difference between this embodiment and the above-mentioned embodiment is that the AZ63 magnesium alloy is subjected to the same pretreatment as described in the embodiment 1, and then placed in the chemical compound conversion solution for treatment. Ce salt 12g·L -1 , Potassium permanganate 1.5g L -1 , Potassium perchlorate 0.3g L -1 , strontium chloride 1.0g·L -1 , boric acid 5g·L -1 , Phytic acid 0.2g L -1 , Sodium dodecylbenzenesulfonate wetting agent 0.6g L -1 , the temperature is room temperature, and the treatment time is 3 minutes; after the reaction is completed, rinse with deionized water, dry naturally, and store in a dry place. The surface of the treated AZ63 magnesium alloy forms a layer of golden yellow conversion film with ideal corrosion resistance, which shows that it has passed the 96-hour neutral salt spray test (ASTM B117), reaching 8 grades.
PUM
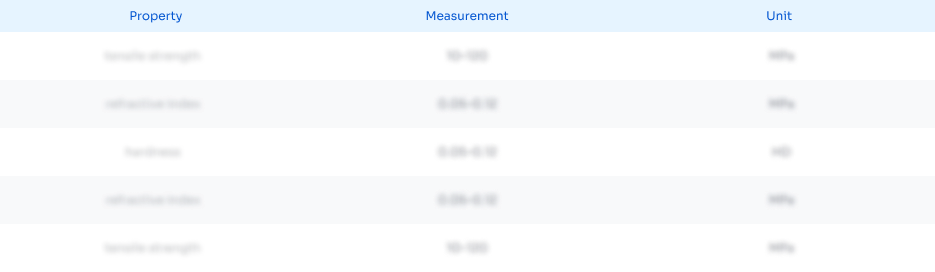
Abstract
Description
Claims
Application Information

- Generate Ideas
- Intellectual Property
- Life Sciences
- Materials
- Tech Scout
- Unparalleled Data Quality
- Higher Quality Content
- 60% Fewer Hallucinations
Browse by: Latest US Patents, China's latest patents, Technical Efficacy Thesaurus, Application Domain, Technology Topic, Popular Technical Reports.
© 2025 PatSnap. All rights reserved.Legal|Privacy policy|Modern Slavery Act Transparency Statement|Sitemap|About US| Contact US: help@patsnap.com