Silicon thin-film photocell electric pole pattern and etching method
A technology of electrode patterns and photovoltaic cells, which is applied in the direction of circuits, electrical components, and climate sustainability, can solve problems such as environmental and equipment pollution, complex processes, and impact on battery electrical performance, and achieve low equipment investment, simplified processes, and improved products. quality effect
- Summary
- Abstract
- Description
- Claims
- Application Information
AI Technical Summary
Problems solved by technology
Method used
Image
Examples
example 1
[0048] image 3 It is a schematic diagram of this embodiment, an amorphous silicon solar cell, the shape is a common and commonly used solar cell, and there are several equidistant corrosion isolation lines. according to image 3shape, prepare the wire mesh. Take 50 grams of deionized water, 10 grams of copper sulfate, 20 grams of ferric chloride, and 0.5 grams of ammonium persulfate, add them to the container one by one, stir to dissolve, then add 30 grams of starch, stir to thicken, then add 0.3 grams of defoamer W-090 and 10 grams of absolute ethanol are stirred to make etching ink. Etching ink is screen-printed onto the surface of the aluminum film. Place it horizontally for 3 minutes, so that the aluminum film on the etching line reacts completely with the etching ink, and there is no breakpoint on the etching line. Bake in a 100°C oven for 30 minutes. After cooling, rinse the ink and metal impurities on the aluminum film with clean water. Soak in clean water for 40...
example 2
[0050] Figure 4 , which is a circular solar cell, used in products with circular windows, such as clocks and other electronic products. There is a circular window in the middle of the solar cell, and there are corrosion isolation lines beside it. First, prepare Figure 4 Shaped wire mesh. Take 55 grams of water, 8 grams of copper sulfate, and 22 grams of ferric chloride, and add them to the container in turn. After stirring, add 35 grams of starch, stir and thicken, then add 11 grams of absolute ethanol and 0.5 grams of defoamer W- 090, made of etching ink after stirring. Slip-print the etching ink on the surface of the aluminum film and place it horizontally for 5 minutes. After the aluminum film is completely corroded, put it in an oven at 80°C for 40 minutes. After cooling, rinse the aluminum film with clean water for 1 minute, so that the impurities on the corrosion line and the corrosion surface of the aluminum film are completely washed away, and then soak in a clea...
PUM
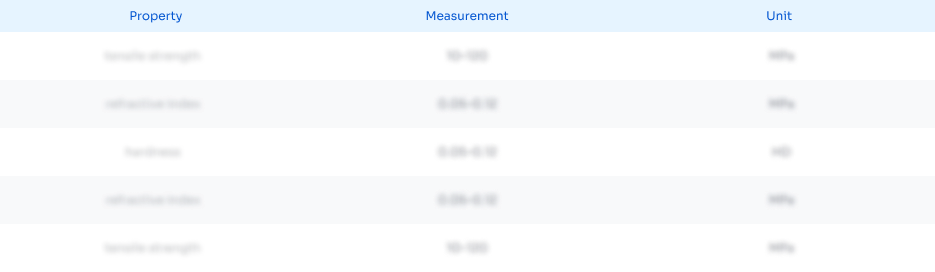
Abstract
Description
Claims
Application Information

- R&D Engineer
- R&D Manager
- IP Professional
- Industry Leading Data Capabilities
- Powerful AI technology
- Patent DNA Extraction
Browse by: Latest US Patents, China's latest patents, Technical Efficacy Thesaurus, Application Domain, Technology Topic, Popular Technical Reports.
© 2024 PatSnap. All rights reserved.Legal|Privacy policy|Modern Slavery Act Transparency Statement|Sitemap|About US| Contact US: help@patsnap.com