Method for preparing white light fluorescent powder used for near ultraviolet LED
A phosphor and near-ultraviolet technology, applied in chemical instruments and methods, luminescent materials, and the use of gas discharge lamps, can solve problems such as lumen efficiency and color reproduction effects, and achieve mild experimental conditions, good reproducibility, Simple and easy method
- Summary
- Abstract
- Description
- Claims
- Application Information
AI Technical Summary
Problems solved by technology
Method used
Image
Examples
Embodiment 1
[0022] Weigh 0.363 g of gadolinium oxide and 0.007 g of europium oxide as an activator, dissolve them in 5 ml of concentrated nitric acid and heat until evaporated to dryness, then dissolve the obtained rare earth nitrate with deionized water to obtain a rare earth nitrate solution. With 0.330 gram of sodium tungstate dihydrate and reaction raw material (0.363 gram of Gd 2 o 3 , 0.007 g Eu 2 o 3 , 0.330 g Na 2 WO 4 2H 2 O) 20 wt% surfactant cetyltrimethylammonium bromide (CTAB) was dissolved in deionized water to obtain a sodium tungstate solution. Mix the obtained rare earth nitrate solution with sodium tungstate solution, and perform magnetic stirring to produce a white precipitate. Control the stirring time for 30 minutes to obtain a white precipitate; transfer the solution containing the precipitate into a 25ml polytetrafluoroethylene reaction kettle, After hydrothermal reaction at 170°C for 48 hours, the reaction product was cooled to room temperature, centrifuged, ...
Embodiment 2
[0024] Weigh 0.398 g of lutetium oxide and 0.007 g of europium oxide as an activator, dissolve them in 5 ml of concentrated nitric acid and heat until evaporated to dryness, then dissolve the obtained rare earth nitrate with 5 ml of deionized water to obtain a rare earth nitrate solution. With 0.326 gram potassium tungstate and be reaction raw material (the Lu that takes by weighing as above 2 o 3 , Eu 2 o 3 , K 2 WO 4 Grams) 18wt% surfactant cetyltrimethylammonium bromide (CTAB) was dissolved in 5ml deionized water to obtain potassium tungstate solution. Mix the rare earth nitrate and potassium tungstate solution, and stir magnetically to produce a white precipitate. The stirring time is 60 minutes, transfer it to a 25ml polytetrafluoroethylene reactor, and conduct a hydrothermal reaction at 120°C for 60 hours. The reaction product is cooled to After room temperature, centrifuge and wash three times with deionized water. Then dry at 70°C for 30 hours to obtain the desir...
Embodiment 3
[0026] Weigh 0.326 g of lanthanum oxide and 0.007 g of europium oxide as an activator, dissolve them in 5 ml of concentrated nitric acid and heat until evaporated to dryness, then dissolve the obtained rare earth nitrate with 5 ml of deionized water to obtain a rare earth nitrate solution. 0.330 gram of sodium tungstate dihydrate and 20wt% surfactant block copolymer (ethylene oxide-propylene oxide-butylene oxide) for reaction raw material (solid raw material as weighed above) are dissolved in deionized In water, sodium tungstate solution was obtained. Mix the obtained rare earth nitrate solution and sodium tungstate solution, stir magnetically to produce a white precipitate, stir magnetically for 40 minutes, transfer it to a 25ml polytetrafluoroethylene reactor at 180°C for hydrothermal reaction for 72 hours, and wait for the reaction product to cool to room temperature , centrifuged and washed three times with deionized water. Then dry at 70°C for 20 hours to obtain the desi...
PUM
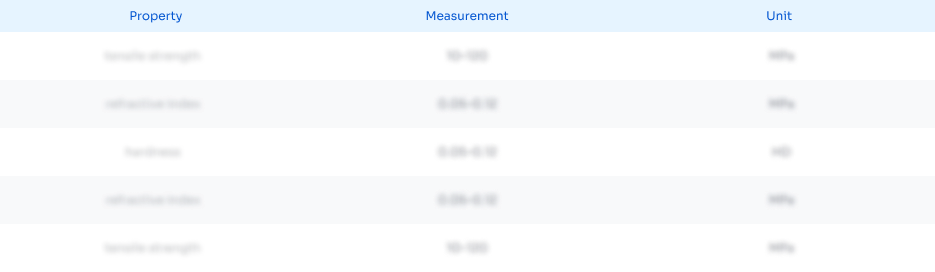
Abstract
Description
Claims
Application Information

- Generate Ideas
- Intellectual Property
- Life Sciences
- Materials
- Tech Scout
- Unparalleled Data Quality
- Higher Quality Content
- 60% Fewer Hallucinations
Browse by: Latest US Patents, China's latest patents, Technical Efficacy Thesaurus, Application Domain, Technology Topic, Popular Technical Reports.
© 2025 PatSnap. All rights reserved.Legal|Privacy policy|Modern Slavery Act Transparency Statement|Sitemap|About US| Contact US: help@patsnap.com