Anti-cracking reinforced ecological cement
A technology of ecological cement and reinforced fiber, which is applied in the field of building materials, can solve the problems of inability to inhibit plastic shrinkage cracking, large water demand, and long-term non-condensation, so as to inhibit the generation and development of micro-cracks, hinder the formation of settlement cracks, Reduces the effect of early thermal cracks
- Summary
- Abstract
- Description
- Claims
- Application Information
AI Technical Summary
Problems solved by technology
Method used
Image
Examples
Embodiment Construction
[0021] A crack-resistant reinforced ecological cement prepared with Portland cement clinker as the base material, using various industrial waste residues and crack-resistant reinforcement materials. It is made of the following raw materials: Portland cement clinker, fly ash, and ferroalloy Slag, boiler slag, slag, grinding aid, gypsum, inorganic mineral reinforced fiber material, polymer fiber.
[0022] The following examples and test data are used to illustrate:
[0023] Table-1 is four independent examples of the anti-cracking reinforced ecological cement of the present invention. Compared with PO42.5 grade cement, and under the same conditions, the setting time, flexural resistance, compression resistance, and splitting tensile strength of the cement are tested. strength. The setting time is carried out according to the method of GB / T1346-2001, and the flexural and compressive strength are all carried out in accordance with the regulations of GB / T17671-1999 except that the wate...
PUM
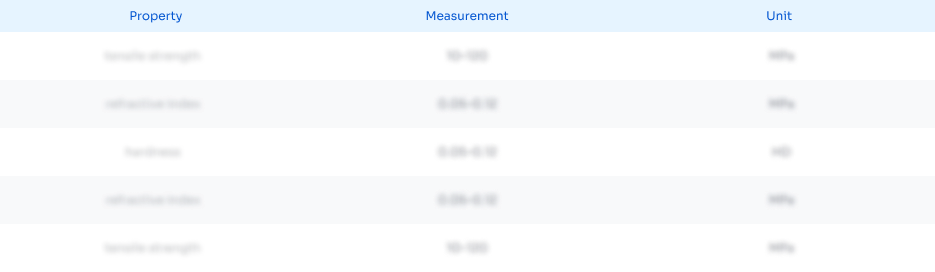
Abstract
Description
Claims
Application Information

- Generate Ideas
- Intellectual Property
- Life Sciences
- Materials
- Tech Scout
- Unparalleled Data Quality
- Higher Quality Content
- 60% Fewer Hallucinations
Browse by: Latest US Patents, China's latest patents, Technical Efficacy Thesaurus, Application Domain, Technology Topic, Popular Technical Reports.
© 2025 PatSnap. All rights reserved.Legal|Privacy policy|Modern Slavery Act Transparency Statement|Sitemap|About US| Contact US: help@patsnap.com