Ready mixed dry mortar and preparation method thereof
A dry-mixed mortar and fine sand technology, which is applied in the field of dry-mixed mortar, can solve the problems of low level of civilized construction, unstable mortar quality, and single type of mortar, so as to facilitate the growth of cement strength and mixing construction, flexible formula, The effect of low drying shrinkage
- Summary
- Abstract
- Description
- Claims
- Application Information
AI Technical Summary
Problems solved by technology
Method used
Examples
Embodiment 1
[0033] The dry-mixed mortar of the present invention is composed of 19.5% of composite Portland cement marked as P.C 32.5, 80% of natural river sand with a fineness modulus of 1.6-2.3 and 0.5% of methyl cellulose ether.
[0034] Dry the medium-fine sand naturally, and then screen out the particles larger than 4.75mm, and weigh them for later use; weigh the cellulose ether polymer and cement, mix them evenly, and set aside; the medium-fine sand after sieving The mixture with cellulose ether polymer and cement is put into a mixer and stirred evenly to obtain a dry-mixed mortar with a strength grade of M10.
Embodiment 2
[0036] The dry-mixed mortar of the present invention is composed of 20% of Portland cement marked P.I32.5, 79.3% of natural river sand with a fineness modulus of 1.6-2.3 and 0.7% of hydroxypropyl methylcellulose ether.
[0037] Dry the medium-fine sand naturally, and then screen out the particles larger than 4.75mm, and weigh them for later use; weigh the cellulose ether polymer and cement, mix them evenly, and set aside; the medium-fine sand after sieving The mixture with cellulose ether polymer and cement is put into a mixer and stirred evenly to obtain a dry-mixed mortar with a strength grade of M10.
Embodiment 3
[0039] The dry-mixed mortar of the present invention is composed of 18% ordinary Portland cement with a label of P.O 32.5, 80% of natural river sand with a fineness modulus of 1.6-2.3 and 2% of methyl cellulose ether and hydroxypropyl methyl cellulose A mixture of ethers.
[0040] Dry the medium-fine sand naturally, and then screen out the particles larger than 4.75mm, and weigh them for later use; weigh the cellulose ether polymer and cement, mix them evenly, and set aside; the medium-fine sand after sieving The mixture with cellulose ether polymer and cement is put into a mixer and stirred evenly to obtain a dry-mixed mortar with a strength grade of M10.
PUM
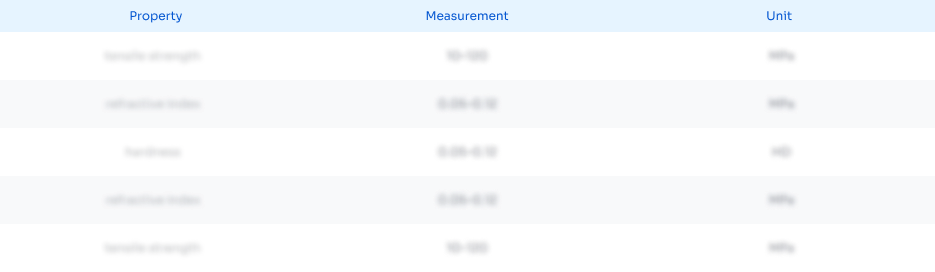
Abstract
Description
Claims
Application Information

- R&D
- Intellectual Property
- Life Sciences
- Materials
- Tech Scout
- Unparalleled Data Quality
- Higher Quality Content
- 60% Fewer Hallucinations
Browse by: Latest US Patents, China's latest patents, Technical Efficacy Thesaurus, Application Domain, Technology Topic, Popular Technical Reports.
© 2025 PatSnap. All rights reserved.Legal|Privacy policy|Modern Slavery Act Transparency Statement|Sitemap|About US| Contact US: help@patsnap.com