Metal anti-corrosion rinsing liquid used for semiconductor manufacture process
A cleaning liquid and semiconductor technology, applied in the field of cleaning liquid, can solve the problems of adverse effects of subsequent processes, narrow cleaning use range, insufficient cleaning efficiency, etc., and achieve the effects of improving flatness quality, reducing surface pitting, and reducing defects
- Summary
- Abstract
- Description
- Claims
- Application Information
AI Technical Summary
Problems solved by technology
Method used
Image
Examples
Embodiment 1
[0040] A cleaning solution (pH=2.4) containing 2% citric acid (citric acid) and 10 ppm of polyacrylic acid (molecular weight: 5000) and water as the balance was used on the copper / silicon dioxide surface polished by the chemical mechanical polishing solution. (1) The process of polishing copper metal with chemical mechanical polishing liquid is: down pressure 1.0-2.0psi, polishing disc speed 50-70rpm, polishing head speed 70-90rpm, polishing liquid flow rate 200-300ml / min, polishing time 1-2min (2) then under pressure 1.5psi, the rotating speed of polishing disk 25rpm, polishing head rotating speed 25rpm, use traditional cleaning solution and this invention cleaning solution respectively, cleaning solution flow rate is at 300ml / min, polishing time 0.5-1min; (3) use Scrub the wafer surface with cleaning solution and polyvinyl alcohol (PVA) roller brush for 2 minutes, the rotation speed of the roller brush is 300rp, the rotation speed of the cleaning head is 280rpm, and the flow ...
Embodiment 2
[0043] A cleaning solution (pH=2.5) containing 0.5% polyamino polyether group tetramethylene phosphonic acid and water as the balance is used on the copper / silicon dioxide surface polished by the chemical mechanical polishing solution. (1) The process of polishing copper metal with chemical mechanical polishing liquid is: down pressure 1.0-2.0psi, polishing disc speed 50-70rpm, polishing head speed 70-90rpm, polishing liquid flow rate 200-300ml / min, polishing time 1-2min (2) then under pressure 1.5psi, the rotating speed of polishing disk 25rpm, polishing head rotating speed 25rpm, use traditional cleaning solution and this invention cleaning solution respectively, cleaning solution flow rate is at 300ml / min, polishing time 0.5-1min; (3) use Scrub the wafer surface with cleaning solution and polyvinyl alcohol (PVA) roller brush for 2 minutes, the rotation speed of the roller brush is 300rp, the rotation speed of the cleaning head is 280rpm, and the flow rate of cleaning solutio...
Embodiment 3
[0046] A cleaning solution (pH=2.5) containing 0.2% methanesulfonic acid, polyacrylic acid (molecular weight 5000) 5000ppm and water as the balance was used on the copper / silicon dioxide surface polished by the chemical mechanical polishing solution. (1) The process of polishing copper metal with chemical mechanical polishing liquid is: down pressure 1.0-2.0psi, polishing disc speed 50-70rpm, polishing head speed 70-90rpm, polishing liquid flow rate 200-300ml / min, polishing time 1-2min (2) then under pressure 1.5psi, the rotating speed of polishing disk 25rpm, polishing head rotating speed 25rpm, use traditional cleaning solution and this invention cleaning solution respectively, cleaning solution flow rate is at 300ml / min, polishing time 0.5-1min; (3) use Scrub the wafer surface with cleaning solution and polyvinyl alcohol (PVA) roller brush for 2 minutes, the rotation speed of the roller brush is 300rp, the rotation speed of the cleaning head is 280rpm, and the flow rate of c...
PUM
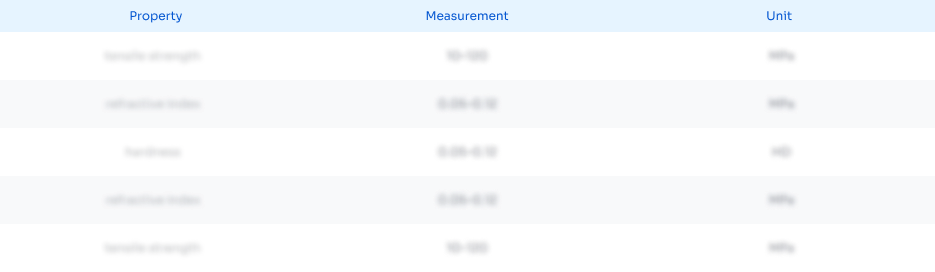
Abstract
Description
Claims
Application Information

- R&D
- Intellectual Property
- Life Sciences
- Materials
- Tech Scout
- Unparalleled Data Quality
- Higher Quality Content
- 60% Fewer Hallucinations
Browse by: Latest US Patents, China's latest patents, Technical Efficacy Thesaurus, Application Domain, Technology Topic, Popular Technical Reports.
© 2025 PatSnap. All rights reserved.Legal|Privacy policy|Modern Slavery Act Transparency Statement|Sitemap|About US| Contact US: help@patsnap.com