High-calcium non-silicon aluminium calcium magnesium ferrous alloy for steel-smelting deoxidization and method for preparing the same
A ferroalloy, silicon-aluminum technology, applied in the field of high-calcium silicon-free aluminum-calcium-magnesium-iron alloy and its preparation, can solve the problems that it is difficult to control the alloy without silicon impurities, oxidation loss, floating volatilization and the like
- Summary
- Abstract
- Description
- Claims
- Application Information
AI Technical Summary
Problems solved by technology
Method used
Examples
Embodiment 1
[0024] Prepare high-calcium silicon-free aluminum-calcium-magnesium-iron alloy of the present invention according to the following steps:
[0025] (1) Al40% by weight, Ca60% and Al60%, Mg40% batching, and smelting into aluminum-calcium master alloy and aluminum-magnesium master alloy respectively with low-frequency induction furnace, standby;
[0026] (2) Calculate the amount of raw material aluminum, aluminum-calcium master alloy, aluminum-magnesium master alloy and low-carbon (C<0.05%) scrap steel used for smelting a furnace by alloy composition content Ca15%, Al15%, Mg2%, Fe68%, and Weigh respectively, put the weighed aluminum-calcium master alloy and aluminum-magnesium master alloy into a high-temperature-resistant container with a mesh (the container can be made of a steel cylinder with graphite on the surface, and a mesh is opened on the surrounding wall, and the upper part with handle,), spare;
[0027] (3) Melting the raw material aluminum and scrap steel in (2) into ...
Embodiment 2
[0033] The preparation method is the same as in Example 1, except that in step (2) by weight Ca15%, Al30% (Al: Ca=2: 1), Mg3%, Fe52% calculate and weigh raw materials. Finally, a high-calcium silicon-free aluminum-calcium-magnesium-iron alloy with component contents of Ca15%, Al30%, Mg3%, and Fe52% is prepared. The number is 2# alloy.
Embodiment 3
[0035] The preparation method is the same as in Example 1, except that in step (2) by weight Ca28%, Al28% (Al: Ca=1: 1), Mg2%, Fe42% calculate and weigh raw materials. Finally, a high-calcium silicon-free aluminum-calcium-magnesium-iron alloy with component contents of Ca28%, Al28%, Mg2%, and Fe42% is prepared. The number is 3# alloy.
PUM
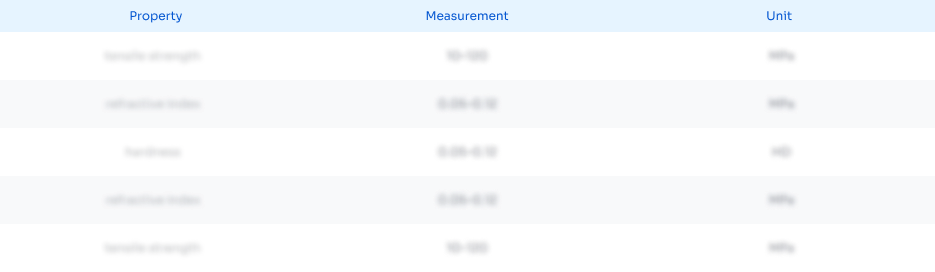
Abstract
Description
Claims
Application Information

- R&D
- Intellectual Property
- Life Sciences
- Materials
- Tech Scout
- Unparalleled Data Quality
- Higher Quality Content
- 60% Fewer Hallucinations
Browse by: Latest US Patents, China's latest patents, Technical Efficacy Thesaurus, Application Domain, Technology Topic, Popular Technical Reports.
© 2025 PatSnap. All rights reserved.Legal|Privacy policy|Modern Slavery Act Transparency Statement|Sitemap|About US| Contact US: help@patsnap.com