Producing technology for microcrystalline cellulose with waste acid cotton linter
A technology of microcrystalline cellulose and production technology, which is applied in the regeneration of pulping liquid, fiber raw material treatment, papermaking, etc., can solve environmental water source pollution and other problems, achieve high cellulose content, facilitate discharge standards, and broaden applications field effect
- Summary
- Abstract
- Description
- Claims
- Application Information
AI Technical Summary
Problems solved by technology
Method used
Examples
Embodiment 1
[0031] a. Soaking: send the waste acid cashmere into the soaking tank through a mechanical feeder for soaking treatment, add the bleaching liquid and rinsing wastewater discharged from the bleaching process into the soaking tank for recycling, and then stir at a stirring speed of 10 revolutions per minute. Make the concentration of the slurry in the pool at 6%, and pre-bleach the waste acid cashmere for 60 minutes;
[0032] b. Removal of slag: The soaked waste acid cashmere is stripped of various impurities after absorbing water and swelling. Use a slag remover to remove impurities by swirling at an inlet pressure of 0.3MPa, and use a centrifugal sieve with a 0.8mm aperture to remove the waste Impurities in acid fleece;
[0033] c, bleaching: waste acid velvet pulp concentration: 8%, use chlorine dioxide as bleaching agent, sodium hydroxide as neutralizer, and adopt DED (chlorine dioxide section + alkali section + chlorine dioxide section) to carry out three sections Bleachin...
Embodiment 2
[0043] a. Soaking: Send the waste acid cashmere into the soaking tank for soaking treatment, add the bleaching liquid and rinsing wastewater discharged from the bleaching process into the soaking tank for recycling, and then stir at a stirring speed of 15 revolutions per minute to make the slurry concentration at 5 %, do pre-bleaching treatment to waste acid cashmere, time 30 minutes;
[0044] b. Removal of slag: soaked waste acid velvet is stripped of various impurities after absorbing water and swelling. Use a slag remover to remove impurities by swirling at an inlet pressure of 0.5MPa, and use a centrifugal sieve with a 1mm aperture to remove waste acid velvet. impurities in
[0045] c, bleaching: waste acid velvet pulp concentration: 10%, use ozone as bleaching agent, sodium carbonate as neutralizing agent, and adopt DEZ (chlorine dioxide section+alkali section+ozone section) to carry out three-stage bleaching, bleaching agent concentration : 0.7%, dosage: 10kg / t slurry; ...
Embodiment 3
[0054] a. Soaking: Send the waste acid cashmere into the soaking tank for soaking treatment, add the bleaching solution and rinsing wastewater discharged from the bleaching process into the soaking tank for recycling, and then stir at a stirring speed of 30 revolutions per minute to make the slurry concentration at 4 %, do pre-bleaching treatment to waste acid cashmere, time 40 minutes;
[0055] b. Removal of slag: The soaked waste acid cashmere is stripped of various impurities after absorbing water and swelling. Use a slag remover to remove impurities by swirling at an inlet pressure of not less than 0.4MPa, and use a centrifugal sieve with a 1.5mm aperture to remove impurities. Remove impurities in waste acid wool;
[0056] c, bleaching: waste acid velvet pulp concentration: 15%, use hydrogen peroxide as bleaching agent, sodium bicarbonate as neutralizer, and adopt PEZ (hydrogen peroxide section+alkali section+ozone section) to carry out three-stage bleaching, Bleaching ag...
PUM
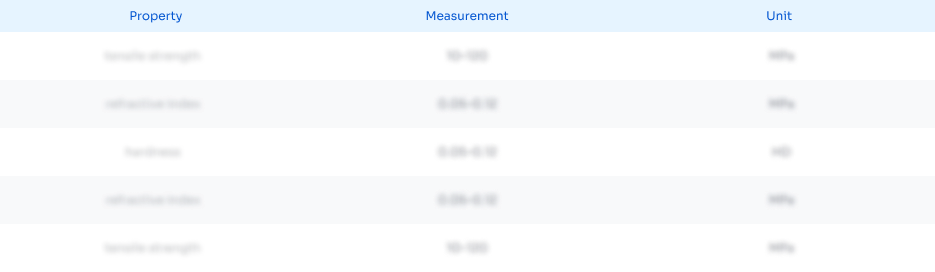
Abstract
Description
Claims
Application Information

- R&D
- Intellectual Property
- Life Sciences
- Materials
- Tech Scout
- Unparalleled Data Quality
- Higher Quality Content
- 60% Fewer Hallucinations
Browse by: Latest US Patents, China's latest patents, Technical Efficacy Thesaurus, Application Domain, Technology Topic, Popular Technical Reports.
© 2025 PatSnap. All rights reserved.Legal|Privacy policy|Modern Slavery Act Transparency Statement|Sitemap|About US| Contact US: help@patsnap.com