Method of preparing foam glass based on boric sludge
A technology of foam glass and boron mud, which is applied in the field of functional inorganic materials, can solve the problem of small dosage, and achieve the effect that is conducive to circular economy and sustainable development
- Summary
- Abstract
- Description
- Claims
- Application Information
AI Technical Summary
Problems solved by technology
Method used
Examples
Embodiment 1
[0016] Grind and pulverize 100g of waste glass to 100-200 mesh, then mix with 40-70g of demagnesia boron mud, heat to 900-1300°C, keep warm for 20-40min; after quenching, grind it into glass powder; then add 3-15g of sodium carbonate, 1-5g of borax, 2-6g of sodium phosphate, put into the mold, and sinter according to the following sintering system: start to heat up to 530-570°C at a speed of 20-25°C / min, keep the temperature for 20-30min, and continue to heat up to 760-800°C ℃, constant temperature for 30-40min, then cooling at 25-30℃ / min to 500-550℃, constant temperature for 50-70min, and finally annealing at 1.5-5℃ / min to 100-200℃, the product blank has good foaming effect, Without cracking, it belongs to thermal insulation foam glass. Product performance: apparent density: 160±30Kg / m3; water absorption: 0.5±0.4vol%; average cell diameter: 1.2±0.4mm; thermal conductivity: 0.060±0.030w / m.k.
PUM
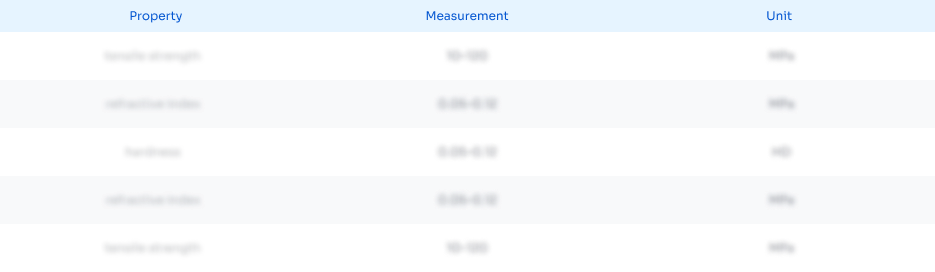
Abstract
Description
Claims
Application Information

- Generate Ideas
- Intellectual Property
- Life Sciences
- Materials
- Tech Scout
- Unparalleled Data Quality
- Higher Quality Content
- 60% Fewer Hallucinations
Browse by: Latest US Patents, China's latest patents, Technical Efficacy Thesaurus, Application Domain, Technology Topic, Popular Technical Reports.
© 2025 PatSnap. All rights reserved.Legal|Privacy policy|Modern Slavery Act Transparency Statement|Sitemap|About US| Contact US: help@patsnap.com