Combustion quality analysis and control system for industrial kiln
A combustion quality, industrial furnace technology, applied in the control of combustion, lighting and heating equipment, etc., can solve the problems of furnace hole flame channeling, reducing combustion temperature, excessive air distribution, etc., achieving great environmental protection benefits and reducing oxidation burning loss , to ensure the effect of burning
- Summary
- Abstract
- Description
- Claims
- Application Information
AI Technical Summary
Problems solved by technology
Method used
Image
Examples
Embodiment 1
[0017] As shown in accompanying drawing 1, the described industrial kiln combustion quality analysis and control system is also called low-oxygen combustion control system. N (an integer of N≥1) burners 11 are installed on the furnace body of the furnace 1 , one end of the burner 11 is connected to the fuel regulating valve 10 , and the other end of the burner 11 communicates with the hearth of the furnace 1 . The kiln 1 can be selected from a heating furnace or a hot blast furnace or a boiler or other fuel-burning kilns. The fuel entering the burner 11 through the fuel regulating valve 10 can be gaseous fuel (such as coke oven gas, blast furnace gas, converter gas, producer gas or its mixed gas, natural gas, liquefied gas, etc.), liquid fuel (such as heavy oil, diesel oil, etc.) ) or solid fuel (such as pulverized bituminous coal or anthracite or lump coal, etc.). There is a flue 2 at the tail of the kiln 1, and a heat exchanger 3 is installed in the flue 2. An air regulati...
Embodiment 2
[0020]As shown in Figure 2, N (an integer of N ≥ 1) burners 11 are installed on the body of the furnace 1, one end of the burner 11 is connected to the fuel regulating valve 10, and the other end of the burner 11 is connected to the furnace 1 There is a flue 2 at the end of the kiln 1, and a heat exchanger 3 is installed in the flue 2. An air regulating valve 9 is installed at the air inlet of the burner 11. The air valve throttle 9 is connected to the outlet of the heat exchanger 3 through the hot air pipe 7, and the inlet of the heat exchanger 3 is connected to the air suction port 5 through the cold air pipe 6. The blower unit 4 has a bypass valve 8 between the cold air pipe 6 and the hot air pipe 7 . Oxygen sensor 21 is installed in the inner cavity of furnace kiln 1, and oxygen sensor 21 can select high-temperature oxygen sensor for use. The signal output end of the oxygen sensor 21 is connected with the acquisition signal input end of the controller 22, the control disp...
PUM
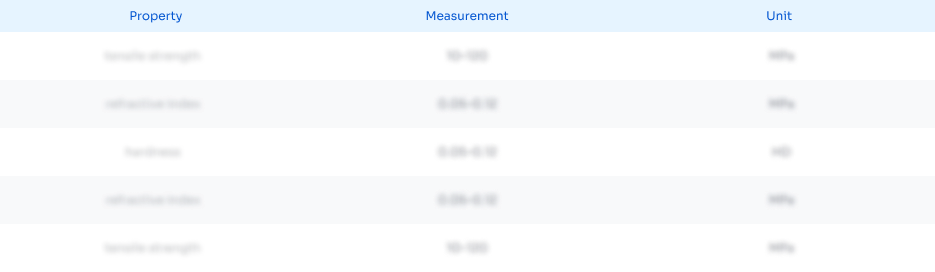
Abstract
Description
Claims
Application Information

- Generate Ideas
- Intellectual Property
- Life Sciences
- Materials
- Tech Scout
- Unparalleled Data Quality
- Higher Quality Content
- 60% Fewer Hallucinations
Browse by: Latest US Patents, China's latest patents, Technical Efficacy Thesaurus, Application Domain, Technology Topic, Popular Technical Reports.
© 2025 PatSnap. All rights reserved.Legal|Privacy policy|Modern Slavery Act Transparency Statement|Sitemap|About US| Contact US: help@patsnap.com