Flow for separating outflow from hydrogenation reaction
A hydrogenation reaction and effluent technology, applied in the direction of effluent separation, etc., can solve the problems of no heat recovery, low energy recovery and utilization rate, complex separation system, etc., and achieve high energy recovery and utilization rate, platform The effect of reduction and simple process
- Summary
- Abstract
- Description
- Claims
- Application Information
AI Technical Summary
Problems solved by technology
Method used
Image
Examples
Embodiment 1 and comparative example 1
[0029] Below through the embodiment a certain 150×10 4 The hydrogenation reaction effluent in the t / a hydrocracking process is compared with the present invention and the existing scheme to further illustrate the technical effect of the present invention.
Embodiment 1
[0030] Embodiment 1 according to the process of the present invention ( figure 1 ) operation, comparative example 1 according to the existing process ( figure 2 )operate.
[0031] In Example 1 and Comparative Example 1, the temperature of the hydrocracking reaction effluent after preliminary heat exchange is 288° C., the pressure is 16.3 MPa, the flow rate is 335,830 kg / h, and the enthalpy value is 101,970 KW.
[0032] In embodiment 1, the operating temperature of the hot high-pressure separator 1 is 288°C, the heat load of the heat exchanger A6 is 22612KW, the operating temperature of the medium-temperature high-pressure separator 2 is 166°C, and the heat load of the air cooler 7 is 17719KW (unavailable heat), the operating temperature of the cold high-pressure separator 3 is 49°C. The heat exchange tower 4 adopts 15 theoretical trays, and the feed ports of the three kinds of streams are respectively arranged at the top, the middle (the 9th theoretical plate) and the botto...
Embodiment 2 and comparative example 2
[0051] Below through the embodiment a certain 150×10 4 The hydrogenation reaction effluent in the t / a coking whole distillate oil hydro-upgrading process is compared with the present invention and the existing scheme (the calculation result of the process simulation software PRO II), further illustrating the technical effect of the present invention.
PUM
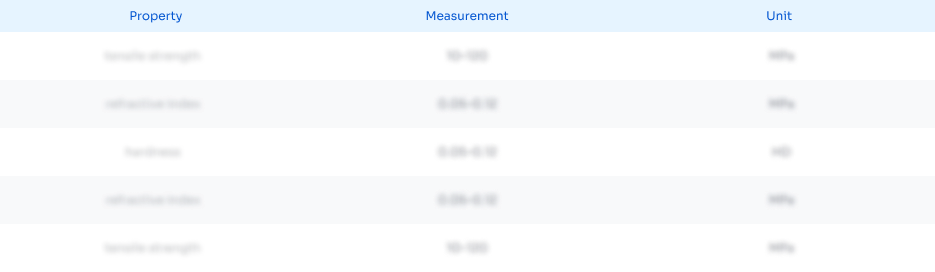
Abstract
Description
Claims
Application Information

- Generate Ideas
- Intellectual Property
- Life Sciences
- Materials
- Tech Scout
- Unparalleled Data Quality
- Higher Quality Content
- 60% Fewer Hallucinations
Browse by: Latest US Patents, China's latest patents, Technical Efficacy Thesaurus, Application Domain, Technology Topic, Popular Technical Reports.
© 2025 PatSnap. All rights reserved.Legal|Privacy policy|Modern Slavery Act Transparency Statement|Sitemap|About US| Contact US: help@patsnap.com