Thermosetting fluorine powder coating resin and its preparing method
A powder coating and thermosetting technology, applied in powder coatings, coatings, etc., can solve the problems of high resin manufacturing cost, complex process, and difficult operation control, etc., achieve excellent construction performance, simple synthesis process, and reduce production costs.
- Summary
- Abstract
- Description
- Claims
- Application Information
AI Technical Summary
Problems solved by technology
Method used
Examples
Embodiment 1
[0059] A 2L high-pressure reaction kettle with electromagnetic stirring is used. There is a jacket heating and cooling device inside the kettle, and an electric heating device is attached to the outer wall of the kettle. Before the experiment, the high-pressure reaction kettle was vacuumed and deoxidized, and the oxygen concentration in the kettle was less than 45ppm. Then, 1092.0g trifluorotrichloroethane, 300.0g deoxygenated deionized water, 123.1g vinyl butyrate, 51.0g hydroxybutyl vinyl ether, 81.1g vinyl tertiary carbonate, 7.0g methacrylic acid, replace twice with high-purity nitrogen in the kettle, remove residual oxygen in the recovery solution, feed 219.0g chlorotrifluoroethylene, while stirring, slowly heat up, when When the temperature rises to 35°C, add 3.5g of diisobutyryl peroxide with a high-pressure metering pump to maintain the reaction temperature between 33 and 37°C. After 4 hours, cool the autoclave with water to stop the reaction, and discharge the remainin...
Embodiment 2
[0063] The operation steps and equipment are the same as in Example 1, except that the difference from Example 1 is: add 936.0g trifluorotrichloroethane, 400.0g deoxygenated deionized water, 61.1g vinyl acetate, 53.0g hydroxypropyl vinyl ether, 84.2g Vinyl tert-carbonate, 11.0g undecylenic acid. 242.0 g of chlorotrifluoroethylene was introduced. When the temperature rises to 50°C, add 15.5g of diisopropyl peroxydicarbonate with a high-pressure metering pump to maintain the reaction temperature between 48 and 52°C. After 8 hours, cool the autoclave with water to stop the reaction, and discharge the remaining residue in the reaction kettle. Unreacted monomer. Add 600.0 g of deionized water to the kettle twice, and recover the solvent by distillation under reduced pressure. Finally, 406.0 g of granular polymer was obtained. The experimental data and the physical properties of the copolymers are listed in Table 1.
Embodiment 3
[0065] A 2L high-pressure reaction kettle with electromagnetic stirring is used. There is a jacket heating and cooling device inside the kettle, and an electric heating device is attached to the outer wall of the kettle. Before the experiment, the high-pressure reactor was vacuumed and deoxidized, and the oxygen concentration was less than 45ppm, and then 750.0g deoxygenated deionized water, 68.8g vinyl acetate, 42.2g hydroxyethyl vinyl ether, 109.2g tertiary vinyl carbonate, 3.7g undecene were added acid, replace the kettle with high-purity nitrogen twice to remove the residual oxygen in the recovery solution, feed 250.0g tetrafluoroethane, then feed 233.0g chlorotrifluoroethylene, and slowly heat up while stirring, when the temperature When the temperature rises to 55°C, use a high-pressure metering pump to add 12.7g of dicyclohexyl peroxydicarbonate to maintain the reaction temperature between 53 and 57°C. After 6 hours, cool the autoclave with water to stop the reaction, an...
PUM
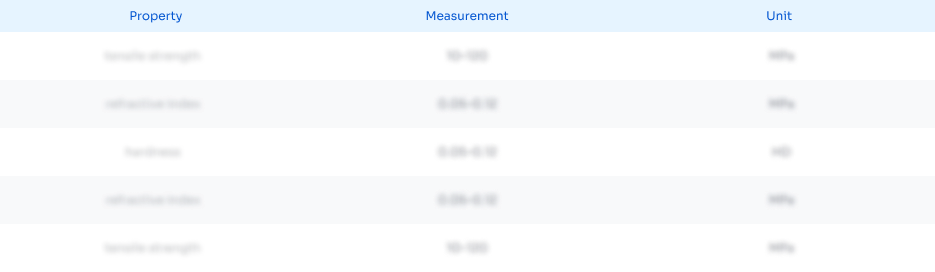
Abstract
Description
Claims
Application Information

- R&D
- Intellectual Property
- Life Sciences
- Materials
- Tech Scout
- Unparalleled Data Quality
- Higher Quality Content
- 60% Fewer Hallucinations
Browse by: Latest US Patents, China's latest patents, Technical Efficacy Thesaurus, Application Domain, Technology Topic, Popular Technical Reports.
© 2025 PatSnap. All rights reserved.Legal|Privacy policy|Modern Slavery Act Transparency Statement|Sitemap|About US| Contact US: help@patsnap.com