Method for making inner deposited and outer hung heat insulating coating for wall
A wall and cladding technology, which is applied to the field of the production of internal pouring and external hanging wall thermal insulation cladding, can solve the problems of increased system load, increased thermal insulation cladding load, waste of raw materials, etc., and achieves increased safety factor and excellent thermal insulation performance. , Improve the effect of thermal insulation
- Summary
- Abstract
- Description
- Claims
- Application Information
AI Technical Summary
Problems solved by technology
Method used
Image
Examples
Embodiment 1
[0045] Embodiment 1: The light-weight plastering mortar is formed by mixing component A and component B according to the ratio of 1:1.5. The component A contains 400Kg of water, 1Kg of water-retaining agent, 600Kg of alkali-resistant emulsion, 3Kg of antifungal agent and 2Kg defoamer; the B component contains 500Kg of cement, 50Kg of 20-120 mesh vitrified floating beads, 450Kg of 20-120 mesh quartz sand, 20Kg of inorganic or organic anti-cracking fiber, 3Kg of waterproofing agent, 1Kg of cement antifreeze, 1Kg of cement superplasticizer and 1Kg of cement early strength agent.
Embodiment 2
[0046] Example 2: The light-weight plastering mortar is formed by mixing component A and component B according to the ratio of 1:4.5. The component A contains 800Kg of water, 10Kg of water retaining agent, 200Kg of alkali-resistant emulsion, 0.5 Kg of antifungal agent and 0.2Kg of defoamer; the B component contains 100Kg of cement, 200Kg of 20-120 mesh vitrified floating beads, 700Kg of 20-120 mesh quartz sand, and 3Kg of inorganic or organic anti-cracking Fiber, 0.3Kg of waterproofing agent, 0.2Kg of cement antifreeze, 0.2Kg of cement water reducing agent and 0.2Kg of cement early strength agent.
Embodiment 3
[0047] Embodiment 3: The light-weight plastering mortar is formed by mixing component A and component B according to the ratio of 1:3. The component A contains 600Kg of water, 5Kg of water-retaining agent, 400Kg of alkali-resistant emulsion, 1.5 Kg of antifungal agent and 1Kg of defoamer; the B component contains 300Kg of cement, 120Kg of 20-120 mesh vitrified floating beads, 580Kg of 20-120 mesh quartz sand, and 10Kg of inorganic or organic crack-resistant fibers , 1.5Kg of waterproofing agent, 0.6Kg of cement antifreeze, 0.6Kg of cement superplasticizer and 0.6Kg of cement early strength agent.
[0048] e. Make a finishing layer outside the lightweight protective mortar layer.
[0049] After the light protective mortar layer is dry, the common practice is to scrape the flexible water-resistant putty, brush the waterproof elastic primer, and paint construction. The enhanced method is to paste the facing bricks.
[0050] The construction tools used are polyurethane pouring m...
PUM
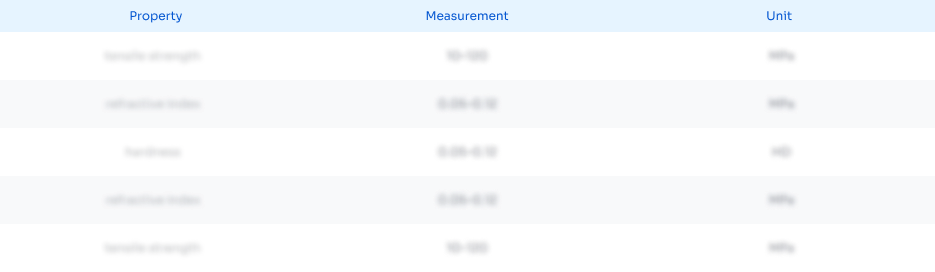
Abstract
Description
Claims
Application Information

- R&D
- Intellectual Property
- Life Sciences
- Materials
- Tech Scout
- Unparalleled Data Quality
- Higher Quality Content
- 60% Fewer Hallucinations
Browse by: Latest US Patents, China's latest patents, Technical Efficacy Thesaurus, Application Domain, Technology Topic, Popular Technical Reports.
© 2025 PatSnap. All rights reserved.Legal|Privacy policy|Modern Slavery Act Transparency Statement|Sitemap|About US| Contact US: help@patsnap.com