Preparation of double axial structured CeO2 film from inorganic salt as raw material by liquid phase chemical process
A thin film technology and inorganic salt technology are applied in the field of preparation of biaxially textured CeO2 thin films, which can solve the problems of high cost of organic cerium salts, inability to prepare dense, uniform and flat biaxially textured thin films, etc. Good quality, good sol stability, cost reduction effect
- Summary
- Abstract
- Description
- Claims
- Application Information
AI Technical Summary
Problems solved by technology
Method used
Image
Examples
preparation example Construction
[0036] 3. CeO 2 Film preparation
[0037] 1) Spin coating, dip coating or spray drying method is used to coat the surface of the substrate to form a film. Spin coating method: the speed of spin coating is from 1000 rpm to 6000 rpm, and the spin coating time is 6 seconds to 3 minutes; When coating, the substrate stays in the sol for 3 seconds to 1 minute, and the pulling speed is 10 to 150 mm / min;
[0038] 2) The film-coated substrate was placed in Ar-4%H 2 Heating in the atmosphere or air, the temperature is from 60°C to 500°C, and the time is from 30 seconds to 24 hours for pyrolysis to remove the organic solvent in the film.
[0039] 3) Sintering heat treatment. Heat the pyrolyzed film at a rate of 1-200°C / min to 500°C-1200°C and keep it warm for 3 minutes to 120 hours. By cooling at a rate of 1 / min, CeO with a biaxial texture, uniform and dense, and a thickness of tens of nanometers to several microns can be obtained. 2 film.
Embodiment 1
[0043] Take cerous nitrate hexahydrate [Ce(NO 3 ) 3 ·6H 2 O] 4.34 g, dried under vacuum at 60°C for 24 hours. Add 6 grams of anhydrous acetylacetone, add zeolite, reflux at 100°C for 24 hours, then add anhydrous ethylene glycol methyl ether to bring the total volume to 40 ml, reflux for 24 hours, finally add anhydrous methanol, reflux for 24 hours, and Filter and then add methanol to make the total sol concentration reach 0.25 mol / L. Filter the above sol, seal it and let it stand for more than 48 hours, then it can be used for film coating. Use the above-mentioned sol to coat the film on the YSZ single crystal by spin coating method, and the film spin parameter is 1000rpm×6 seconds+6000rpm×30 seconds. The prepared gel film was dried on a hot table at 400°C for 10 minutes, and then the pyrolyzed film was placed in a three-stage tube furnace with a heating rate of 10°C / min and heat-treated at 1000°C. 1 hour, then the furnace is cooled and the atmosphere is air throughout th...
Embodiment 2
[0045] The preparation process steps are the same as those in Example 1, except that, in the thin film preparation process, the dip coating method is used instead of the spin coating method to coat the film. The process of the dip coating method is to place about 50 ml of the prepared solution in a beaker, clamp the cleaned substrate with the chuck of the dip coating machine, slowly immerse it in the solution, and let it stand for 10 seconds. Pull out from the solution at a uniform speed of 1 mm / s, then perform pyrolysis and heat treatment, and the process is exactly the same as in Example 1. CeO with a thickness of about 100 nm was obtained 2 film.
PUM
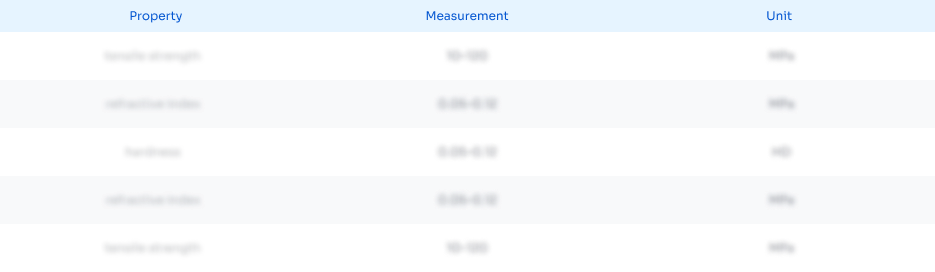
Abstract
Description
Claims
Application Information

- R&D
- Intellectual Property
- Life Sciences
- Materials
- Tech Scout
- Unparalleled Data Quality
- Higher Quality Content
- 60% Fewer Hallucinations
Browse by: Latest US Patents, China's latest patents, Technical Efficacy Thesaurus, Application Domain, Technology Topic, Popular Technical Reports.
© 2025 PatSnap. All rights reserved.Legal|Privacy policy|Modern Slavery Act Transparency Statement|Sitemap|About US| Contact US: help@patsnap.com