Three-dimensional ladar module with alignment reference insert circuitry
a three-dimensional ladar module and alignment reference technology, applied in the field of laserradar imaging technology, can solve the problems of undesirable sensor types, lack of circuit speed and capacity to achieve very high (i.e., centimeter) range resolution and sensitivity, etc., to achieve enhanced imaging capability, reduce layer-to-layer or channel-to-channel “jitter”, and increase detector output processing circuit density
- Summary
- Abstract
- Description
- Claims
- Application Information
AI Technical Summary
Benefits of technology
Problems solved by technology
Method used
Image
Examples
Embodiment Construction
[0033]Turning now to the figures wherein like numerals designate like elements among the several views, FIG. 1 shows a block diagram of the present invention.
[0034]A photon source, such as a laser 1, generates a beam pulse 5, which is directed toward a scene or target 7, through suitable beam-shaping optics 10.
[0035]In a preferred embodiment, laser 1 is a 1064 nm, mechanically aligned, 300 micro-Joule, seed YAG laser capable of producing a pulse width of 500 picoseconds. In the preferred embodiment, a beam amplifier is provided (not shown), such as a master oscillator power amplifier, wherein a seed beam is fed into the amplifier. In this preferred embodiment, the seed beam passes through a Faraday rotator and enters a four-pass, thermally-controlled amplifier which includes two pumped YAG diodes.
[0036]In the preferred embodiment, beam-shaping optics 10 is a beam-shaping holographic lens suitable for projecting a rectangular beam area on a target. It has been determined that a recta...
PUM
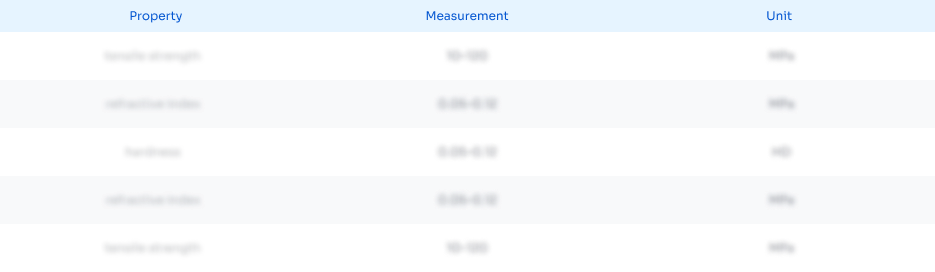
Abstract
Description
Claims
Application Information

- R&D Engineer
- R&D Manager
- IP Professional
- Industry Leading Data Capabilities
- Powerful AI technology
- Patent DNA Extraction
Browse by: Latest US Patents, China's latest patents, Technical Efficacy Thesaurus, Application Domain, Technology Topic, Popular Technical Reports.
© 2024 PatSnap. All rights reserved.Legal|Privacy policy|Modern Slavery Act Transparency Statement|Sitemap|About US| Contact US: help@patsnap.com