Epitaxial wafer and method of manufacturing the same
- Summary
- Abstract
- Description
- Claims
- Application Information
AI Technical Summary
Benefits of technology
Problems solved by technology
Method used
Image
Examples
example 1
[0096]In Example 1, an Si layer having a predetermined thickness was epitaxially grown on a wafer sliced from a CZ single-crystalline wafer having a diameter of 300 mm and mirror-finished. In Examples 2 to 6, a heat treatment was performed for the same sample as that of Example 1 at 1,000° C. / 0.5 hrs under an Ar atmosphere using an upright furnace. In Examples 7 to 12, a heat treatment was performed at 1,150° C. / 30 sec under an Ar atmosphere using an RTA process furnace. Then, the wafer obtained through the heat treatment was ground from the surface side to produce samples by a predetermined thickness. The specifications of the samples are shown in Table 1 as follows.
TABLE 1Substrate OxygenEpi LayerGrindingSurface OxygenConcentrationThicknessThicknessConcentrationAmount of(E17atoms / cc)(μm)Heat Treatment(μm)(E17atoms / cc)DislocationExample 113.22N / AN / AUndetectableCExample 213.121000° C. / 0.5 hr0.31.2BExample 313.221000° C. / 0.5 hr13.3AExample 413.241000° C. / 0.5 hr0.3UndetectableCExample...
example 2
[0103]In Example 2, an Si layer having a predetermined thickness was epitaxially grown on a wafer sliced from a CZ single-crystalline wafer having a diameter of 300 mm and mirror-finished. The thickness of the grown epitaxial layer was 4 μm. Then, various kinds of heat treatments were performed. The heat treatment was performed in an RTA furnace under an oxidizing atmosphere if the treatment time is 180 sec or less. Meanwhile, the heat treatment was performed in an upright furnace under a mixture gas atmosphere (N2 and O2 (O2=10%)) if the treatment time is 180 sec or more. After the heat treatment, the generated oxide film was removed using a diluted HF solution, and a stress loading test was performed in a way similar to Example 1. The result is shown in FIG. 9.
[0104]According to the result, it is understood that the oxygen concentration of the epitaxial layer becomes high because the surface of the epitaxial layer is oxidized under an oxidizing atmosphere, the oxygen is inwardly d...
PUM
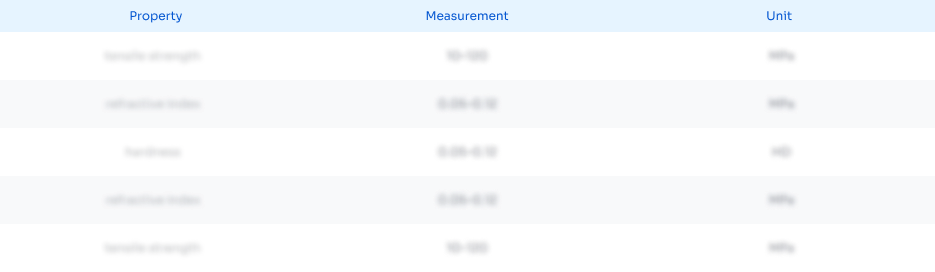
Abstract
Description
Claims
Application Information

- R&D
- Intellectual Property
- Life Sciences
- Materials
- Tech Scout
- Unparalleled Data Quality
- Higher Quality Content
- 60% Fewer Hallucinations
Browse by: Latest US Patents, China's latest patents, Technical Efficacy Thesaurus, Application Domain, Technology Topic, Popular Technical Reports.
© 2025 PatSnap. All rights reserved.Legal|Privacy policy|Modern Slavery Act Transparency Statement|Sitemap|About US| Contact US: help@patsnap.com