Liquid-Vapor Separating Method and a Liquid-Vapor Separating Type Evaporator
a liquid-vapor separation and separating method technology, applied in the direction of indirect heat exchangers, separation processes, lighting and heating apparatus, etc., can solve the problems of reducing the efficiency of surface enhancement, affecting the efficiency of heat exchange formation, and the inner wall of the tube cannot be well wetted by liquid, so as to reduce the consumption of materials, improve the efficiency of energy conversion and utilization, and reduce the power of the compressor
- Summary
- Abstract
- Description
- Claims
- Application Information
AI Technical Summary
Benefits of technology
Problems solved by technology
Method used
Image
Examples
embodiment 1
A Liquid-Vapor-Separation-Outside-Spiral-Tube Evaporator
[0034]As shown in FIG. 4, the present embodiment comprises a spiral outer tube 1, and an inner tube 2 positioned in the outer tube 1, the inner tube 2 of present embodiment is an inner tube bundle with spiral configuration (as shown in FIG. 5), which can effectively improve the wetting and disturbance of the liquid while enhancing the heat exchange and the evaporation of the thin liquid film. As shown in FIG. 4, both ends of the outer tube 1 connect the outer wall of the inner tube 2 hermetically, the bottom port of the inner tube 2 is used as the inlet 21 of heating fluid, the top port of the inner tube 2 is used as the outlet 22 of heating fluid, and the steam outlet 11 of the outer tube 1 is positioned at the tube wall of the top port of the outer tube 1. Between the upmost outer tube 1 and the inner tube 2, an annular separation plate is set as a separation device 3 which partitions the outer tube 1 into a superheat segment...
embodiment 2
A Liquid-Vapor-Separation-Outside-Vertical-Serpentine-Tube Evaporator
[0037]As shown in FIG. 6, the main difference between this embodiment and the embodiment 1 lies in that the present embodiment employs a vertical serpentine outer tube 1 and a corresponding inner tube 2 as a separation device 3 positioned between the layer 1 and layer 2, and makes the first layer of outer tube 1 a superheat segment 12 and the downstream of the second layer of outer tube 1 an evaporation segment 13. Alternatively, the separation device can be positioned between the third layer and the fourth layer, and the actual position of the separation device can be determined according to requirement of the superheat degree. A liquid-vapor-separation tube 4 is connected to the superheat segment 12 near the separation device 3, and a steam drainage tube 5 connects the liquid-vapor-separation tube 4 with each layer of outer tube 1 at the evaporation segment 13. An incoming tube 6 for evaporated liquid connects to...
embodiment 3
A Liquid-Vapor-Separation-Inside-Vertical-Serpentine-Air-Heating Evaporator
[0039]As shown in FIG. 7, the present embodiment has a vertical serpentine tube similar to that of embodiment 2, but a single layer tube referred to as inner tube 2 is employed due to air used as heating fluid. Outside fins 7 are set between each layer of inner tube 2 via expanded joints, and the separation device 3 partitions the outer tube 2 into superheat segment 23 and evaporation segment 24. The exact position of separation segment 3 can be determined according to the requirement of the superheat degree. The top port of the inner tube 2 is steam outlet 25, and the bottom port is closed, and the inner tube 2 is connected to the lower portion of the incoming tube 6 via a residual liquid recycling tube 14 positioned on the surface of the port. The top of the incoming tube 6 is connected to the evaporation segment 24 near the separation device 3. The top end of the liquid-vapor-separation tube 4 is connected...
PUM
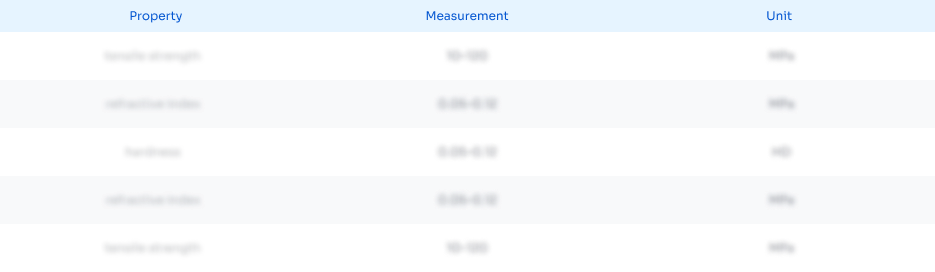
Abstract
Description
Claims
Application Information

- R&D
- Intellectual Property
- Life Sciences
- Materials
- Tech Scout
- Unparalleled Data Quality
- Higher Quality Content
- 60% Fewer Hallucinations
Browse by: Latest US Patents, China's latest patents, Technical Efficacy Thesaurus, Application Domain, Technology Topic, Popular Technical Reports.
© 2025 PatSnap. All rights reserved.Legal|Privacy policy|Modern Slavery Act Transparency Statement|Sitemap|About US| Contact US: help@patsnap.com