System and method for controlling the cooling of variable heat loads in heat generating devices
a variable heat load and heat generating device technology, applied in the field of cooling of electrical, electronic and optical components, can solve the problems of damage to electrical or electronic devices, high temperature and/or large flow rate, and the inability to use sensible heating of fluid to remove heat from electrical and electronic components
- Summary
- Abstract
- Description
- Claims
- Application Information
AI Technical Summary
Benefits of technology
Problems solved by technology
Method used
Image
Examples
Embodiment Construction
[0018]Referring now to FIGS. 1A and 1B, there is illustrated a cooling system 10 which circulates a refrigerant as the working fluid. The refrigerant may be any suitable vaporizable refrigerant, such as R-134a. The cooling cycle can begin at liquid pump 12, shown as a Hermetic Liquid Pump. Pump 12 pumps the liquid phase refrigerant to a liquid manifold 14, where it is distributed to one or a plurality of branches or lines 16. From the manifold 14, each branch or line 16 feeds liquid refrigerant to a cold plate 18. The condensing temperature of the refrigerant is preferably controlled so as to be above the ambient dew point where the cold plate evaporator device is located.
[0019]As illustrated in FIG. 2, each cold plate 18 is in thermal contact with an electrical or electronic component or components 20 to be cooled, causing the liquid refrigerant to evaporate at system pressure. None, some, or all of the liquid refrigerant may evaporate at cold plate 18, depending on how much heat i...
PUM
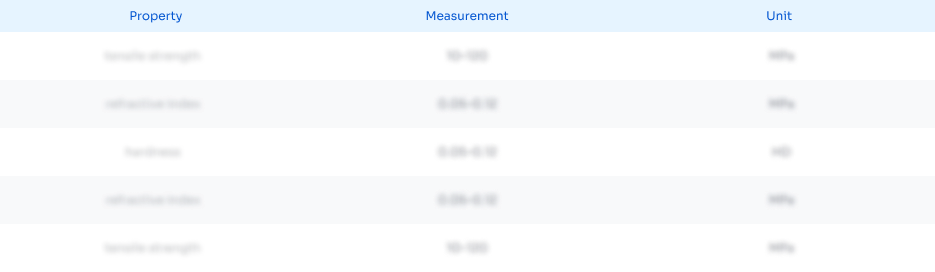
Abstract
Description
Claims
Application Information

- R&D
- Intellectual Property
- Life Sciences
- Materials
- Tech Scout
- Unparalleled Data Quality
- Higher Quality Content
- 60% Fewer Hallucinations
Browse by: Latest US Patents, China's latest patents, Technical Efficacy Thesaurus, Application Domain, Technology Topic, Popular Technical Reports.
© 2025 PatSnap. All rights reserved.Legal|Privacy policy|Modern Slavery Act Transparency Statement|Sitemap|About US| Contact US: help@patsnap.com