Method for the gasification of hydrocarbon feedstocks
a hydrocarbon feedstock and gasification technology, applied in the field of gasification of hydrocarbon feedstocks, can solve the problems of high capital cost of coal gasification plants, prohibitively high gas prices, and too low to be used in manufacturing high-value hydrogen-containing materials that are needed for commerce, and achieve the effect of reducing the capital cost and reducing the production of co2
- Summary
- Abstract
- Description
- Claims
- Application Information
AI Technical Summary
Benefits of technology
Problems solved by technology
Method used
Image
Examples
example 1
[0265] This example illustrates an embodiment of the process that delivers most of the output energy as electricity (726 MW net), however, still produces 100 mM scfd of H2. This example follows the sequence of unit operations as depicted in FIG. 7 and will be described with reference to FIG. 7.
[0266] All reactors have a 6.5 meter hearth diameter and 8.6 meter barrel diameter. There are two metal oxide reduction reactors (e.g., reactor 604) and both have a 50 minute cycle for reducing FeO to Fe and they are staggered in time. There is one metal oxidation reactor (e.g., reactor 602) that has a 25 minute cycle time for oxidizing Fe to FeO. The plant operates 7884 hours per year (i.e., 90 percent availability).
[0267] At the start of the cycle, two metal oxide reduction reactors (referred to as 604a and 604b) each contain 293 tonnes (metric tons) of an alloy comprised of 40% iron and 60% tin, and 540 tonnes of slag comprised of 65% FeO, 12.4% CaO, 15.4% SiO2 and 7.2% ash (all percentag...
example 2
[0303] Example 2 illustrates an embodiment of the process that also makes 100 mM scfd of H2. Through the recovery of fuel-bound H2 (derived from the hydrocarbon feed), this example focuses on recovering all available H2; consequently, less electricity is produced as compared to Example 1. This example follows the sequence of unit operations as depicted in FIG. 8.
[0304] All reactors have a 4.2 meter hearth diameter and 5.6 meter barrel diameter. These reactors are smaller than the reactors of Example 1 as the total pet coke feed (illustrated below) is less for this Example 2. There are two metal oxide reduction reactors 604 (referred to as 604a and 604b); both have a 50 minute cycle for reducing FeO to Fe, and they are operated in a staggered mode. There is one metal oxidation reactor 602; it has a 25 minute cycle time for oxidizing Fe to FeO. The plant operates 7884 hours per year (i.e., 90 percent availability).
[0305] At the start of the cycle, metal oxide reduction reactor 604 c...
example 3
[0346] This Example 3 is directed to maximizing the amount of electricity produced. It derives from Example 1 (FIG. 7). However, the high CO syngas stream from amine scrubber 623 and the high H2 syngas stream from amine scrubber 622 are combined and sent to turbine unit 642, air compressor and gas-fired turbine. Table 49 summarizes the net electricity generated by this Example 3.
TABLE 49Net Salable ProductNet Electrical922MWEnergy for Sale7,269,048MW · hrs
PUM
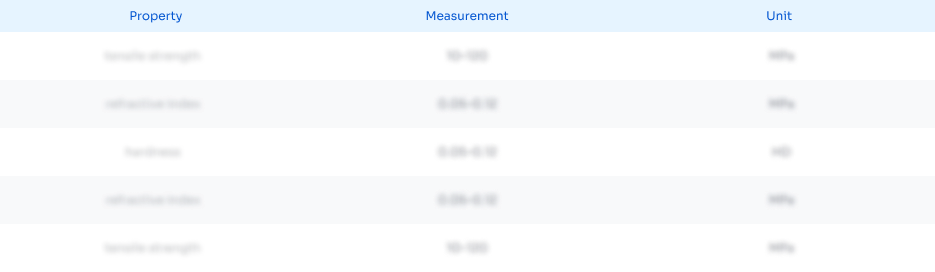
Abstract
Description
Claims
Application Information

- R&D
- Intellectual Property
- Life Sciences
- Materials
- Tech Scout
- Unparalleled Data Quality
- Higher Quality Content
- 60% Fewer Hallucinations
Browse by: Latest US Patents, China's latest patents, Technical Efficacy Thesaurus, Application Domain, Technology Topic, Popular Technical Reports.
© 2025 PatSnap. All rights reserved.Legal|Privacy policy|Modern Slavery Act Transparency Statement|Sitemap|About US| Contact US: help@patsnap.com