Laser loaded 3D micron and nano size forming process and equipment
A three-dimensional forming, micro-nano scale technology, applied in laser welding equipment, nanotechnology, nanotechnology, etc., can solve the problems that restrict the wide application of microfabrication technology
- Summary
- Abstract
- Description
- Claims
- Application Information
AI Technical Summary
Problems solved by technology
Method used
Image
Examples
Embodiment Construction
[0015] Figure 1 shows a schematic diagram of a device for laser loading to realize three-dimensional forming at the micro-nano scale. The details and implementation are described as follows:
[0016] The device for laser loading to realize micro-nano-scale three-dimensional forming consists of a laser loading system and a target clamping system. The laser loading system consists of a nanosecond pulse laser 1 and a convex lens 3. The laser beam 2 emitted by the nanosecond pulse laser 1 is focused by the convex lens and directly enters the target clamping system. The target clamping system consists of a pressing plate 4, an optical glass 5, an absorbing layer 6, a target 7, a template 8, and a target clamping device 9. The pressing plate 4 has a screw mechanism, which can be screwed into the concave hole of the target clamping device 9. Cavity, so that the optical glass 5 can be pressed together, and the target material 7 can be fastened in the concave cavity of the target mater...
PUM
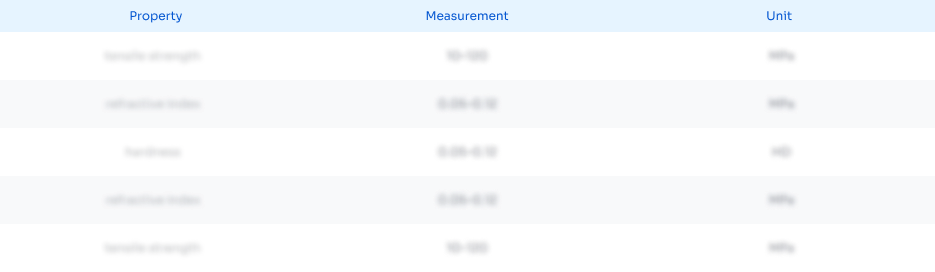
Abstract
Description
Claims
Application Information

- R&D
- Intellectual Property
- Life Sciences
- Materials
- Tech Scout
- Unparalleled Data Quality
- Higher Quality Content
- 60% Fewer Hallucinations
Browse by: Latest US Patents, China's latest patents, Technical Efficacy Thesaurus, Application Domain, Technology Topic, Popular Technical Reports.
© 2025 PatSnap. All rights reserved.Legal|Privacy policy|Modern Slavery Act Transparency Statement|Sitemap|About US| Contact US: help@patsnap.com