Control cooling method of resolving self-break while producing high-carbon wire rod
A technology for controlling cooling and wire rod, applied in the field of steel rolling, can solve problems such as surface shrinkage, natural fracture of wire rod, increase natural fracture, etc., to achieve the effect of increasing surface shrinkage, solving natural fracture, and reducing internal stress
- Summary
- Abstract
- Description
- Claims
- Application Information
AI Technical Summary
Problems solved by technology
Method used
Image
Examples
Embodiment Construction
[0015] At present, the rolling mill used by Shougang to produce 82B series wire rods is the third-generation Morgan rolling mill. The specific water cooling distribution after rolling is shown in Figure 1. Before December 2004, when producing large-size 82B wire rod, see Table 1 for water cooling control requirements after rolling.
[0016] When the workers control the water cooling after rolling, the control method of each worker is different, and the water cooling intensity of the 1, 2# and 3# water tanks cannot be reasonably allocated. The situation of the Φ12.5mm specification wire rod produced at that time is shown in Table 2 shown.
[0017] Table 1, process control without additional pre-water cooling and temperature measuring instrument
[0018]
control item
Rolling temperature
finish rolling temperature
Spend
Spinning temperature
Water cooling control
Control requirements
1020-1060
℃
...
PUM
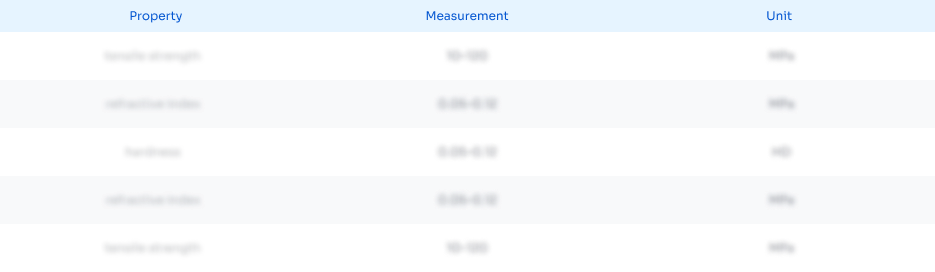
Abstract
Description
Claims
Application Information

- R&D
- Intellectual Property
- Life Sciences
- Materials
- Tech Scout
- Unparalleled Data Quality
- Higher Quality Content
- 60% Fewer Hallucinations
Browse by: Latest US Patents, China's latest patents, Technical Efficacy Thesaurus, Application Domain, Technology Topic, Popular Technical Reports.
© 2025 PatSnap. All rights reserved.Legal|Privacy policy|Modern Slavery Act Transparency Statement|Sitemap|About US| Contact US: help@patsnap.com