Method for silane reinforcing magnesium alloy cathode electrophoretic corrosion-proof layer
A technology for enhancing magnesium alloys and cathodic electrophoresis, which is applied to metal material coating processes, coatings, electrolytic coatings, etc. It can solve the problems of limited size and high cost of magnesium alloy samples, and achieve easy mass and automated production and production costs. Low, the effect of improving corrosion resistance
- Summary
- Abstract
- Description
- Claims
- Application Information
AI Technical Summary
Problems solved by technology
Method used
Image
Examples
Embodiment 1AZ31
[0032] Example 1 AZ31 wrought magnesium alloy sample silane enhanced cathodic electrophoresis
[0033]Because the cathodic electrophoresis technology has requirements on the surface finish and cleanliness of the sample. Therefore, the surface pretreatment of the magnesium alloy is first required. The process route is: pre-cleaning → degreasing (alkaline washing) → hot water washing → cold water washing → pickling → water washing → silane treatment → drying. The alkaline washing solution is a mixed solution of 40g / L sodium hydroxide and 10g / L sodium phosphate decahydrate. The degreasing is carried out at 60~70℃. The alkaline time is 3min~30min according to the oil stain of the sample. The acid is carried out immediately after washing. Washing, pickling time depends on the surface roughness of the sample and the formula of the pickling solution, generally 30s to 3min. After pickling, rinse immediately to ensure that the surface is not oxidized, and then immerse the sample with silan...
Embodiment 2AZ91
[0041] Example 2 AZ91D magnesium alloy hand tool shell silane enhanced cathodic electrophoresis
[0042] Firstly, the surface pretreatment of the magnesium alloy is required. The process route is: pre-cleaning→degreasing (alkaline washing)→hot water washing→cold water washing→acid washing→water washing→silane treatment→drying. The alkaline washing solution is a mixed solution of 40g / L sodium hydroxide and 10g / L sodium phosphate decahydrate. Degreasing is carried out at 60-70°C. The alkaline time is 30 minutes according to the amount of oil stain on the sample. Pickling is carried out immediately after washing. The pickling time depends on the surface roughness of the sample and the formula of the pickling solution, generally 3 minutes. After pickling, rinse immediately to ensure that the surface is not oxidized, and then immerse the sample with silane. The silane is γ-glycidoxypropyltrimethoxysilane, the concentration is 2%, and the immersion time is 30s~90s. The immersion tempera...
Embodiment 3AZ91
[0050] Example 3 AZ91D magnesium alloy motorcycle parts silane enhanced cathodic electrophoresis
[0051] Firstly, the surface pretreatment of the magnesium alloy is required. The process route is: pre-cleaning→degreasing (alkaline washing)→hot water washing→cold water washing→acid washing→water washing→silane treatment→drying. The alkaline washing solution is a mixed solution of 40g / L sodium hydroxide and 10g / L sodium phosphate decahydrate. Degreasing is carried out at 60~70℃. The alkaline time is 15min according to the amount of oil stain on the sample. Pickling is carried out immediately after washing. The pickling time depends on the surface roughness of the sample and the formula of the pickling solution, generally 3min. Rinse immediately after pickling to ensure that the surface is not oxidized, and then immerse the sample with silane. The silane is acrylic triethoxysilane, the concentration is 2%, the immersion time is 90s, and the immersion temperature is normal temperatur...
PUM
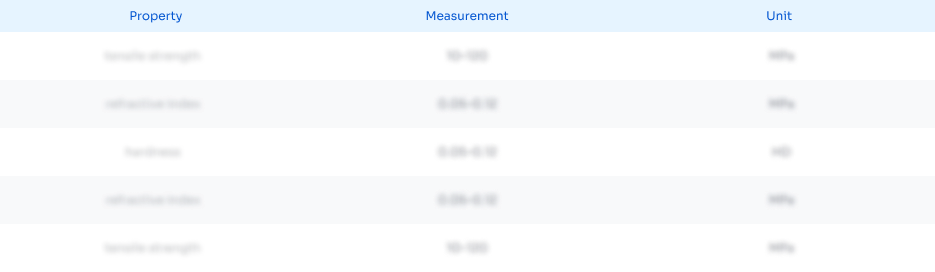
Abstract
Description
Claims
Application Information

- R&D
- Intellectual Property
- Life Sciences
- Materials
- Tech Scout
- Unparalleled Data Quality
- Higher Quality Content
- 60% Fewer Hallucinations
Browse by: Latest US Patents, China's latest patents, Technical Efficacy Thesaurus, Application Domain, Technology Topic, Popular Technical Reports.
© 2025 PatSnap. All rights reserved.Legal|Privacy policy|Modern Slavery Act Transparency Statement|Sitemap|About US| Contact US: help@patsnap.com