Composite SiC and its making process
A manufacturing method and technology of guide rollers, applied in the direction of manufacturing tools, chemical instruments and methods, rollers, etc., can solve the problems of short service life, low cost of guide rollers, low cost performance, etc., and achieve improved wear resistance, low cost, The effect of rich raw materials
- Summary
- Abstract
- Description
- Claims
- Application Information
AI Technical Summary
Problems solved by technology
Method used
Examples
Embodiment 1
[0029] By weight, the composition of the composite material is: 15% SiC, 1.0% Cr, 1.0% Mo, 0.5% Nb, and the total amount of Ti, Ni, Mn, V, Zr, RE, Si or B alloying elements does not exceed 2% , the carbon content in the steel matrix of the composite material is 0.4%, and the balance is Fe; the composite material is made into a Φ5mm wire, which is coated on the metal surface by arc thermal spraying to combine with the metal surface.
Embodiment 2
[0031] By weight, the composition of the composite material is: 15% SiC, 1.0% Cr, 1.0% Mo, 0.5% Nb, and the total amount of Ti, Ni, Mn, V, Zr, RE, Si or B alloying elements does not exceed 2% , the carbon content in the steel matrix of the composite material is 0.4%, and the balance is Fe; the above-mentioned composite material raw materials are mixed and ball-milled to make powder, and the method of plasma spraying is used to coat the metal surface to make it match the metal surface. combine.
Embodiment 3
[0033] By weight, the composition of the composite material is: 15% SiC, 1.0% Cr, 1.0% Mo, 0.5% Nb, and the total amount of Ti, Ni, Mn, V, Zr, RE, Si or B alloying elements does not exceed 2% , the carbon content in the steel matrix of the composite material is 0.4%, and the balance is Fe; the above-mentioned composite material raw materials are mixed and ball-milled to make powder, and coated on the metal surface, melted by laser heating and mixed with the metal surface binding.
[0034] The guide roller is subjected to strong friction and wear during operation, and its surface must have high wear resistance. SiC is an inexpensive hard phase with a Vickers hardness of 33400MPa. The SiC particles are dispersed in the steel matrix. The steel matrix plays the role of bonding and supporting the SiC particles, and the SiC particles play the role of strengthening, hardening and anti-wear. Such composite materials have high wear resistance. Welding a layer of the composite materia...
PUM
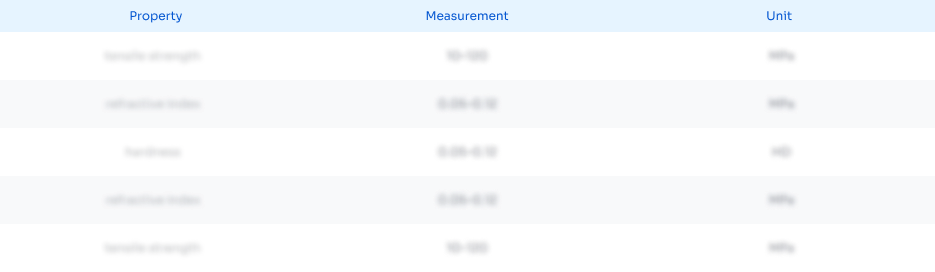
Abstract
Description
Claims
Application Information

- R&D
- Intellectual Property
- Life Sciences
- Materials
- Tech Scout
- Unparalleled Data Quality
- Higher Quality Content
- 60% Fewer Hallucinations
Browse by: Latest US Patents, China's latest patents, Technical Efficacy Thesaurus, Application Domain, Technology Topic, Popular Technical Reports.
© 2025 PatSnap. All rights reserved.Legal|Privacy policy|Modern Slavery Act Transparency Statement|Sitemap|About US| Contact US: help@patsnap.com