Hot rolling cogging process of Ti-Ni alloy ingot
A titanium-nickel alloy and ingot casting technology, applied in metal rolling, metal rolling, metal processing equipment and other directions, can solve the problems of high cost, high comprehensive cost, and low billet yield.
- Summary
- Abstract
- Description
- Claims
- Application Information
AI Technical Summary
Problems solved by technology
Method used
Examples
Embodiment 1
[0011] Using 25kg vacuum induction melting furnace, at 10 -1 Under the condition of a vacuum degree above Pa, the titanium sponge and electrolytic nickel are smelted into a small titanium-nickel alloy ingot with a nominal composition of Ti-50.8at.%Ni, the melting current is 90-110A, and the melting voltage is 280-330V. The size of the ingot is Φ76×450mm, and after peeling, it becomes a smooth ingot of Φ68×450mm.
[0012] The light ingot is heat treated in the electric furnace, and the temperature is raised to 850 ±10 ℃, keep warm for 30min. Then, on the CЩM-175 stepper rolling mill, the billet is directly rolled. The rotation speed of the main motor is 150n / min., the rolling speed is 600mm / min., and the rolling step is 10mm / step; the initial rolling temperature is about 840°C, and the final rolling temperature is about 700°C; the rolling deformation rate is 52%.
[0013] Rolled titanium-nickel alloy rod Φ47 ±1 ×940mm, there are 7-8mm cup-shaped shrinkage pits at both ends,...
Embodiment 2
[0015] The preparation method of the titanium-nickel alloy ingot is the same as above. The light ingot of Φ68×450mm is heat treated in the electric furnace, and the temperature is raised to 950 ±10 ℃, keep warm for 40min. Then, on the CЩM-175 stepper rolling mill, direct billet rolling is carried out. The rotation speed of the main motor is 120n / min., the rolling speed is 480mm / min., and the rolling step is 10mm / step; the initial rolling temperature is about 930°C, and the final rolling temperature is about 700°C; the rolling deformation rate is 74%.
[0016] The rolled titanium-nickel alloy rod is Φ35 ±1 ×1740mm, its elongation factor reached 4. There are 12-15mm cup-shaped shrinkage pits at both ends, but there are no macroscopic defects on the surface. The internal metallographic structure is basically a dynamic recovery recrystallization structure, but there are obvious elongated and deformed grains in the longitudinal direction.
[0017] The direct blanking method fo...
PUM
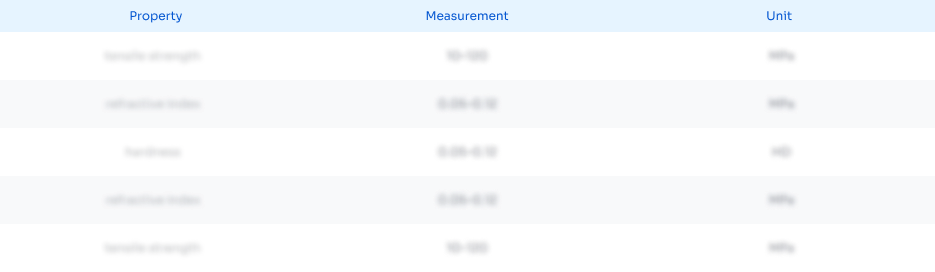
Abstract
Description
Claims
Application Information

- R&D
- Intellectual Property
- Life Sciences
- Materials
- Tech Scout
- Unparalleled Data Quality
- Higher Quality Content
- 60% Fewer Hallucinations
Browse by: Latest US Patents, China's latest patents, Technical Efficacy Thesaurus, Application Domain, Technology Topic, Popular Technical Reports.
© 2025 PatSnap. All rights reserved.Legal|Privacy policy|Modern Slavery Act Transparency Statement|Sitemap|About US| Contact US: help@patsnap.com